Hi all
We have an ASME VIII Vessel with a DN25 NPT tapped hole. We now need to fill the hole and make the OD surface flush. What would be a suitable detail to fill the hole?
Wall thickness 23mm.
We are thinking of the placing a thread plug, then cutting this back to the surface and a seal weld.
Thanks
We have an ASME VIII Vessel with a DN25 NPT tapped hole. We now need to fill the hole and make the OD surface flush. What would be a suitable detail to fill the hole?
Wall thickness 23mm.
We are thinking of the placing a thread plug, then cutting this back to the surface and a seal weld.
Thanks
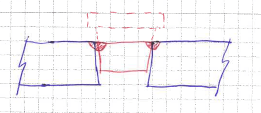