Hello
I am not an expert in the GD&T. I want to know how do you get the values for the position tolerans? are the a standard value or you just choose by yourself?
I really appreciate if someone could explain it. I attach some picture with the red marked values. Those value I am intressted to know how to get?
Regards
NJ
I am not an expert in the GD&T. I want to know how do you get the values for the position tolerans? are the a standard value or you just choose by yourself?
I really appreciate if someone could explain it. I attach some picture with the red marked values. Those value I am intressted to know how to get?
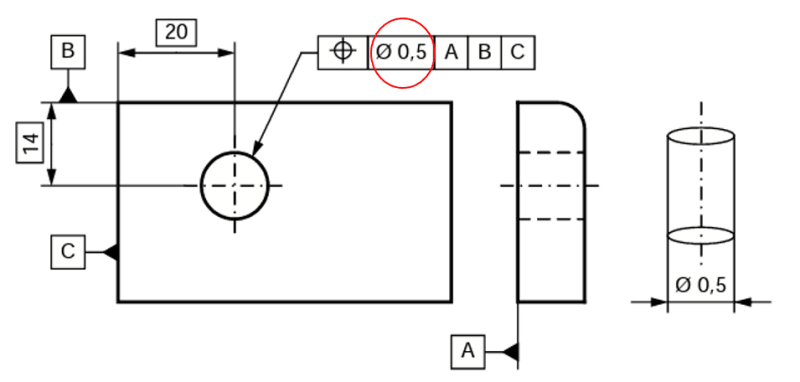
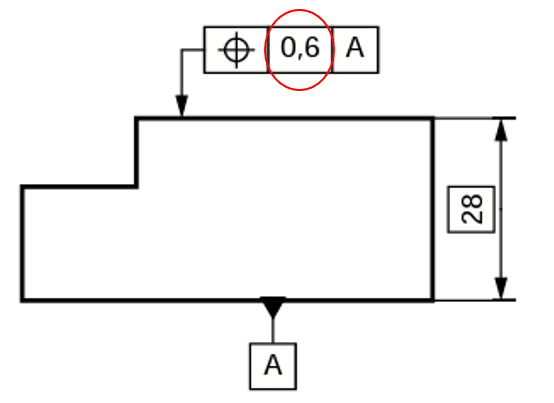
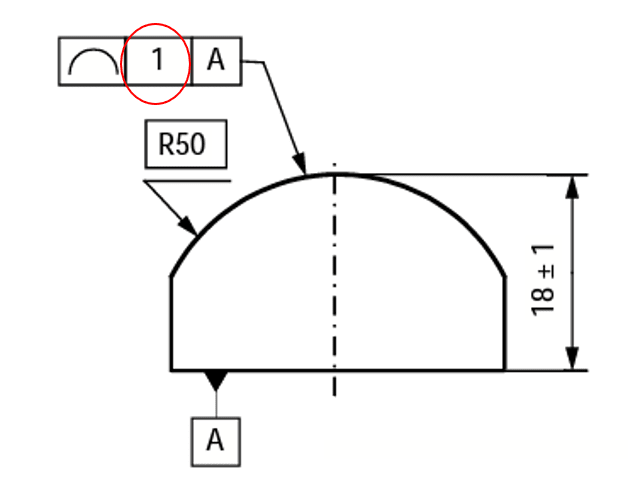
Regards
NJ