RFreund
Structural
- Aug 14, 2010
- 1,885
What is your detail preference for hollow core plank spanning parallel to an exterior wall. Could be a basement wall or just exterior wall. Do you bear on the PC on the wall, or do you provide an angle with slotted holes? Any reason?
EIT
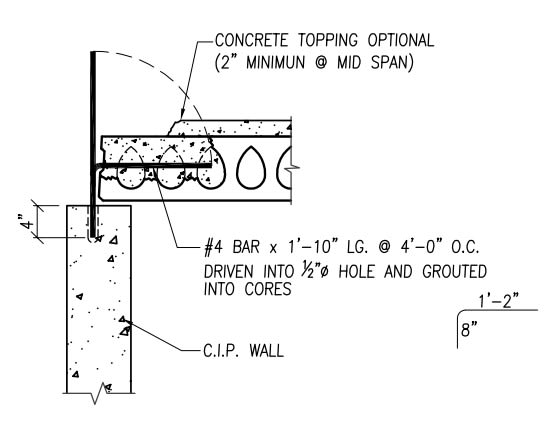
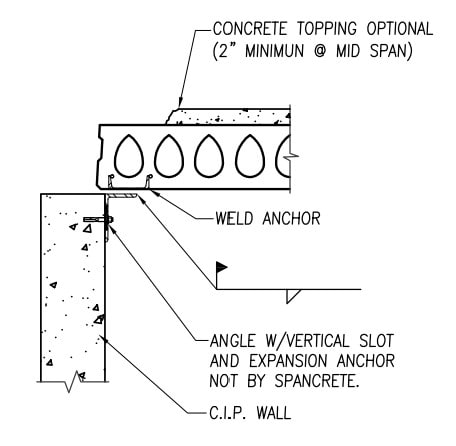
EIT