I’ll preface this by saying that I have absolutely zero engineering experience in high pressure systems, so please cut me some slack. I managed to get some three phase motors cheap, and I have some various pressure washer pumps laying around, so I thought it would be fun to fabricate a parallel pump system with the goal of learning some of the basic principles of hydraulics. If I happen to end up with something that that works well for cleaning up my engine projects and shop, even better!
I’m covered on the electrical & control side – still playing with the design, but to start, I’m planning to build a rotary phase converter and control the motor speeds with variable frequency drives. For the sake of simplicity, the mechanical coupling from the motors to the pumps will be a dampened belt-drive. On the logic side, my plan is to install flow sensor and pressure sensors ahead of the check valves, and a single flow/pressure sensor on the combined line. Each of the sensors will connect to a compute resource (microcontroller, Arduino IDE, or small computer – TBD) for data logging purposes, and the input data will have the ability to control the VFDs.
Here’s a simple diagram:
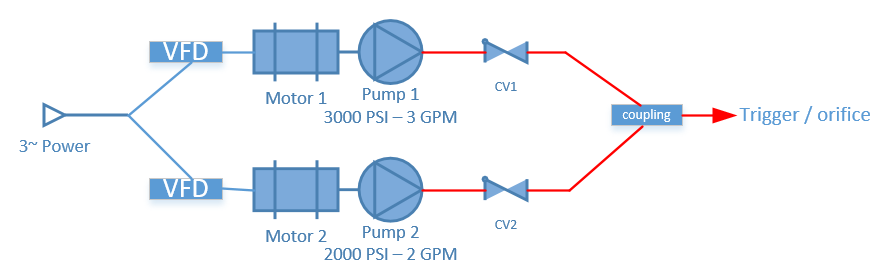
The pumps have integral pressure-actuated unloader valves which will stay in place for the time being.
So to start with the basics, what equations are used to determine flow rate in a parallel coupled system like this one? Assuming that the pumps are spinning at design RPM and producing the PSI/GPM in the diagram, would we use the mean PSI & GPM to calculate the final flow and pressure? E.g – (3000+2000)/ 2 = 2500 PSI, and (3+2)/2 = 2.25 GPM? If this is correct, does it scale without regard to the number of pumps?
Are the check valves actually necessary in a system like this? My thought was that without a check valve on P2, the unloader valve on P2 would stay open, preventing the pump from doing any useful work and pressurizing it beyond its design limit of 2000 PSI. Is this a correct assumption?
Any recommended elementary reading on the subject? Also, I would more than appreciate any design guidance, advice or criticism… new subject matter for me.
Thanks!
I’m covered on the electrical & control side – still playing with the design, but to start, I’m planning to build a rotary phase converter and control the motor speeds with variable frequency drives. For the sake of simplicity, the mechanical coupling from the motors to the pumps will be a dampened belt-drive. On the logic side, my plan is to install flow sensor and pressure sensors ahead of the check valves, and a single flow/pressure sensor on the combined line. Each of the sensors will connect to a compute resource (microcontroller, Arduino IDE, or small computer – TBD) for data logging purposes, and the input data will have the ability to control the VFDs.
Here’s a simple diagram:
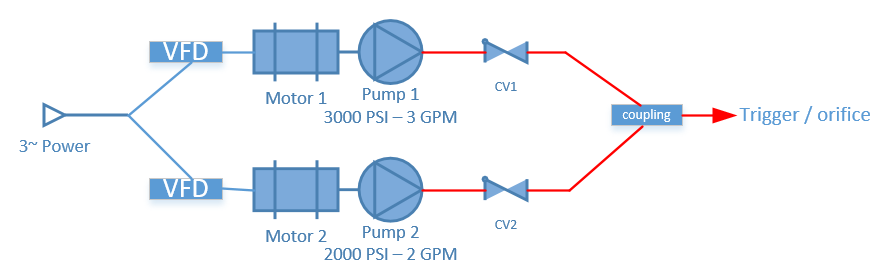
The pumps have integral pressure-actuated unloader valves which will stay in place for the time being.
So to start with the basics, what equations are used to determine flow rate in a parallel coupled system like this one? Assuming that the pumps are spinning at design RPM and producing the PSI/GPM in the diagram, would we use the mean PSI & GPM to calculate the final flow and pressure? E.g – (3000+2000)/ 2 = 2500 PSI, and (3+2)/2 = 2.25 GPM? If this is correct, does it scale without regard to the number of pumps?
Are the check valves actually necessary in a system like this? My thought was that without a check valve on P2, the unloader valve on P2 would stay open, preventing the pump from doing any useful work and pressurizing it beyond its design limit of 2000 PSI. Is this a correct assumption?
Any recommended elementary reading on the subject? Also, I would more than appreciate any design guidance, advice or criticism… new subject matter for me.
Thanks!