CloudNine1
Mechanical
Hi folks,
I'm trying to calculate the required size of a pressure relief valve I will use on a theoretical double pipe heat exchanger.
I've came across these formulas:
But there are a few things I don't really understand there:
1. First and foremost, I'm having a hard time understanding where is the orifice in such valves.
Many pictures of cross-section PRVs don't even use the word orifice when describing the valve's components.
On the following picture, is "valve-seat" (part 2) the actual orifice?
2. Regarding the first formula - what is DeltaP? Yes, it is the pressure drop across the orifice, but which pressure do they refer to?
The difference between the overpressure and the set pressure? It got me confused.
3. Regarding the second formula - they used Q there (volumetric flow of the liquid) but it is a parameter I also don't know! I mean, Q=VA, and on the first formula I found V, but I'm still left with 2 variables (Q and A) and they're just "finding" A by using Q whereas it is still unknown!
Would appreciate your help regarding these matters.
Thanks a lot!
I'm trying to calculate the required size of a pressure relief valve I will use on a theoretical double pipe heat exchanger.
I've came across these formulas:
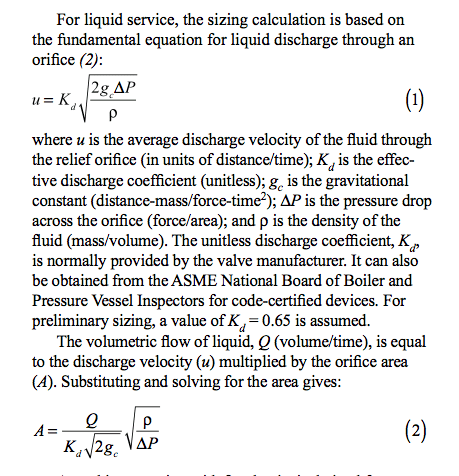
But there are a few things I don't really understand there:
1. First and foremost, I'm having a hard time understanding where is the orifice in such valves.
Many pictures of cross-section PRVs don't even use the word orifice when describing the valve's components.
On the following picture, is "valve-seat" (part 2) the actual orifice?
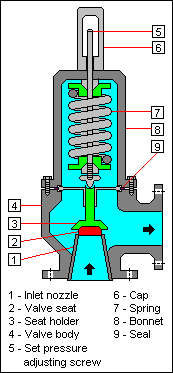
2. Regarding the first formula - what is DeltaP? Yes, it is the pressure drop across the orifice, but which pressure do they refer to?
The difference between the overpressure and the set pressure? It got me confused.
3. Regarding the second formula - they used Q there (volumetric flow of the liquid) but it is a parameter I also don't know! I mean, Q=VA, and on the first formula I found V, but I'm still left with 2 variables (Q and A) and they're just "finding" A by using Q whereas it is still unknown!
Would appreciate your help regarding these matters.
Thanks a lot!