Hi Guys,
Im in the process of adapting the pressure vessel on my air rifle to increase capacity.
Please take a look at the image attached, is it acceptable for a pressure vessel to step down in size from 23.5mm to 20mm, and then back up again to 23.5mm? The step down in size is where 2 halves of the cylinder screw together.
Or is it absolutely necessary for a pressure vessel to be all one continuous size as in the bottom example?
The cylinder stores the pressure at 232bar.
Many Thanks
Im in the process of adapting the pressure vessel on my air rifle to increase capacity.
Please take a look at the image attached, is it acceptable for a pressure vessel to step down in size from 23.5mm to 20mm, and then back up again to 23.5mm? The step down in size is where 2 halves of the cylinder screw together.
Or is it absolutely necessary for a pressure vessel to be all one continuous size as in the bottom example?
The cylinder stores the pressure at 232bar.
Many Thanks
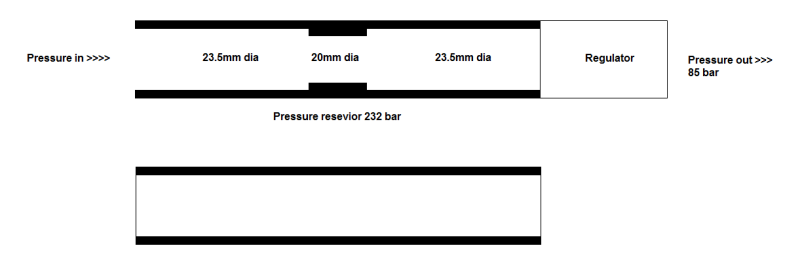