Hi,
Long time no post - and first post in the Corrosion area.
Needing advice on some rather unusual corrosion on the rotor of a progressing cavity pump. I've been working with these more than 20 years now (applications support, tech sales and some service work) and not seen anything quite like this before. We've previously used this materials combination successfully on the "same" product in several other locations. I'd previously considered bentonite to be moderately abrasive (depends on source quality) but not chemically aggressive. Closest I've seen to this in the past is when a client started dosing ferric chloride upstream without telling any one. That is definitely not the case here.
For scale, the rotor diameter is 45mm. It's a 2-stage pump.
The rotor material is induction-hardened C45 tool-steel running against a nitrile stator.
Product is 2% sodium bentonite mixed with towns water (site is in western Austria). Ambient temperature - approx 10 - 15ºC at present.
Pump running speed is ~200 rpm
Flooded suction 1 - 2m with a short, well-sized pipe. Pump runs very smoothly - almost silent. This is not cavitation.
Discharge is 2 Bar against a loading valve and the pump runs 50% 24/7 (duty standby, 2 hour switch over)
First picture (less damage) is after 8 days running. Performance still ok.
Second picture is after 3 weeks. It's still moving product, but the rate is well down.
Also attached is a scan of an analysis done - we were looking for chlorides - didn't find much < 30mg/l. The towns water alone was 4.0 - 5.6 mg/l. pH measured at 8.6
We've switched the rotor on the first pump to 316ss - haven't seen the result of that yet. Also have a 316/hard-chrome plate waiting for the second pump. Hopefully this will make the problem go away, but would really like to understand what the root cause is! Any ideas?
Thanks
Nick
Long time no post - and first post in the Corrosion area.
Needing advice on some rather unusual corrosion on the rotor of a progressing cavity pump. I've been working with these more than 20 years now (applications support, tech sales and some service work) and not seen anything quite like this before. We've previously used this materials combination successfully on the "same" product in several other locations. I'd previously considered bentonite to be moderately abrasive (depends on source quality) but not chemically aggressive. Closest I've seen to this in the past is when a client started dosing ferric chloride upstream without telling any one. That is definitely not the case here.
For scale, the rotor diameter is 45mm. It's a 2-stage pump.
The rotor material is induction-hardened C45 tool-steel running against a nitrile stator.
Product is 2% sodium bentonite mixed with towns water (site is in western Austria). Ambient temperature - approx 10 - 15ºC at present.
Pump running speed is ~200 rpm
Flooded suction 1 - 2m with a short, well-sized pipe. Pump runs very smoothly - almost silent. This is not cavitation.
Discharge is 2 Bar against a loading valve and the pump runs 50% 24/7 (duty standby, 2 hour switch over)
First picture (less damage) is after 8 days running. Performance still ok.
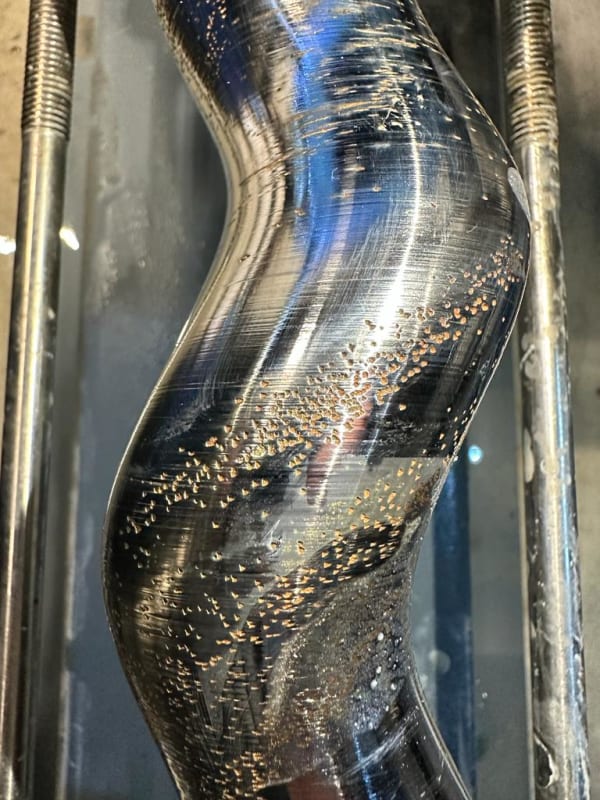
Second picture is after 3 weeks. It's still moving product, but the rate is well down.
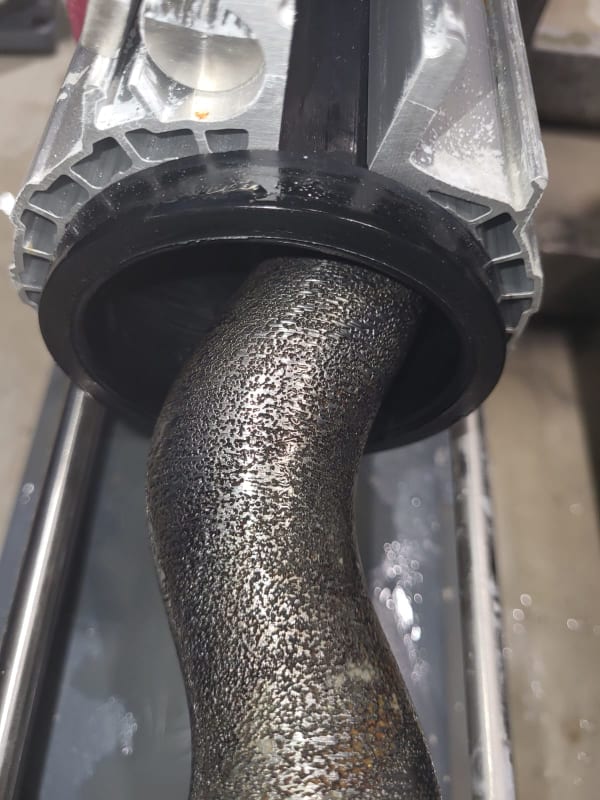
Also attached is a scan of an analysis done - we were looking for chlorides - didn't find much < 30mg/l. The towns water alone was 4.0 - 5.6 mg/l. pH measured at 8.6
We've switched the rotor on the first pump to 316ss - haven't seen the result of that yet. Also have a 316/hard-chrome plate waiting for the second pump. Hopefully this will make the problem go away, but would really like to understand what the root cause is! Any ideas?
Thanks
Nick