Mech5656
Mechanical
- Aug 2, 2014
- 127
Hello Dear Engineers,
As you may have noticed from my other posts, I am working to study pump components damage mechanism. I found another impeller damage due possible cavitation and wanted to share with you to get your feedback on damage mechanisms. This is suction impeller (first stage) for water injection pump that is used in oil field. Noticed the area where impeller ring sits apart from cavitation damage. What can possibly cause that?
As you may have noticed from my other posts, I am working to study pump components damage mechanism. I found another impeller damage due possible cavitation and wanted to share with you to get your feedback on damage mechanisms. This is suction impeller (first stage) for water injection pump that is used in oil field. Noticed the area where impeller ring sits apart from cavitation damage. What can possibly cause that?
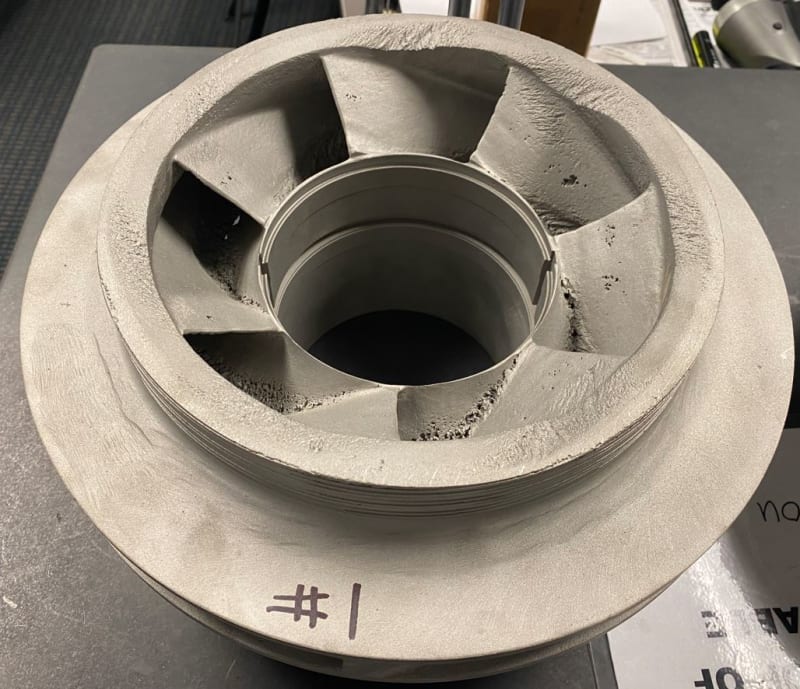