I work at a small site (120ish personnel) that typically works with small pumps, both centrifugal and PD pumps. Motor sizes typically run 3-15 HP. Engineering was not a priority in the site in the past, so were no existing piping standards, much less anything regarding pump installations (pump alignment was a maintenance guy with a straight edge...).
I recently installed a 100 HP pump in a temporary capacity, and expect to move it within a year to a permanent location. This is much larger than anything else on site, and the size and vibration of the pump has raised concerns with me around reliability of the pump (seals, bearings, etc) being affected by insufficient grouting/foundations. Pumps on site have typically been stilt mounted or had bases directly bolted to concrete with no grouting of the bases here. I don't really have much experience with requirements for pump foundations, so am looking for guidance here.
Is there a minimum horsepower requirement for considering grouting? I have found a good guide from BASF on the procedure for actually grouting a pump base (below), but it does not address when grouting is needed. Do you excellent members have any general guidelines or specific calculations that need to be addressed in considering the pump foundation and grouting? When is grouting needed, and what type of grout is acceptable for various horsepower pumps? Is the general procedure found in the link below a broadly applicable one?
Edit (1/8/2020): The two pumps in use are from Sulzer, and include a T-frame metal base. The procedure for securing the pumps is non-standard (see images below). Leveling/raising the pump is accomplished by washer and nuts on the underside of the base on the foundation bolts. A top nut is used on the foundation bolts to then tighten the entire base down. Then everything is encased in concrete/grout. I've spoken with a Sulzer rep, and he confirmed this procedure. It's odd that this design inherently means there is no tensioning force provided by the foundation bolts, as the top nut is tightened against the bottom leveling nut.
I've read through a previous post from many years ago ( members cautioned against this method. Is that still the case?
I recently installed a 100 HP pump in a temporary capacity, and expect to move it within a year to a permanent location. This is much larger than anything else on site, and the size and vibration of the pump has raised concerns with me around reliability of the pump (seals, bearings, etc) being affected by insufficient grouting/foundations. Pumps on site have typically been stilt mounted or had bases directly bolted to concrete with no grouting of the bases here. I don't really have much experience with requirements for pump foundations, so am looking for guidance here.
Is there a minimum horsepower requirement for considering grouting? I have found a good guide from BASF on the procedure for actually grouting a pump base (below), but it does not address when grouting is needed. Do you excellent members have any general guidelines or specific calculations that need to be addressed in considering the pump foundation and grouting? When is grouting needed, and what type of grout is acceptable for various horsepower pumps? Is the general procedure found in the link below a broadly applicable one?
Edit (1/8/2020): The two pumps in use are from Sulzer, and include a T-frame metal base. The procedure for securing the pumps is non-standard (see images below). Leveling/raising the pump is accomplished by washer and nuts on the underside of the base on the foundation bolts. A top nut is used on the foundation bolts to then tighten the entire base down. Then everything is encased in concrete/grout. I've spoken with a Sulzer rep, and he confirmed this procedure. It's odd that this design inherently means there is no tensioning force provided by the foundation bolts, as the top nut is tightened against the bottom leveling nut.
I've read through a previous post from many years ago ( members cautioned against this method. Is that still the case?

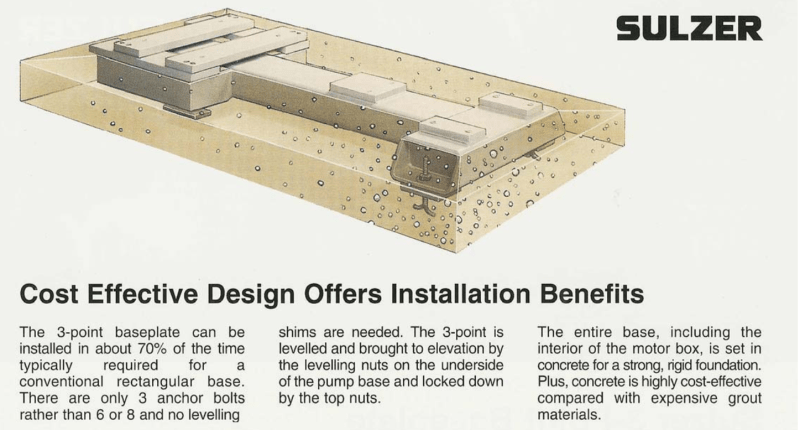