riqson
Mining
- Aug 13, 2017
- 6
Hi all , I am brasilian , sorry about ortografic errors...
someone can help-me to determine how much HP and what RPM must be ideal for my 18" drege pump? pls take a look in anex esqueme ,
is a 1,1 mts x 35 cm 4 blades impeller in a pump shell 1,5 mts diametre
discharge and suction pipes 17" internal diamere
pump from sluice box goes 5 mts head by 9 mts lenght
max deep pum from botton in the river 32 mts
thanks in advance
someone can help-me to determine how much HP and what RPM must be ideal for my 18" drege pump? pls take a look in anex esqueme ,
is a 1,1 mts x 35 cm 4 blades impeller in a pump shell 1,5 mts diametre
discharge and suction pipes 17" internal diamere
pump from sluice box goes 5 mts head by 9 mts lenght
max deep pum from botton in the river 32 mts
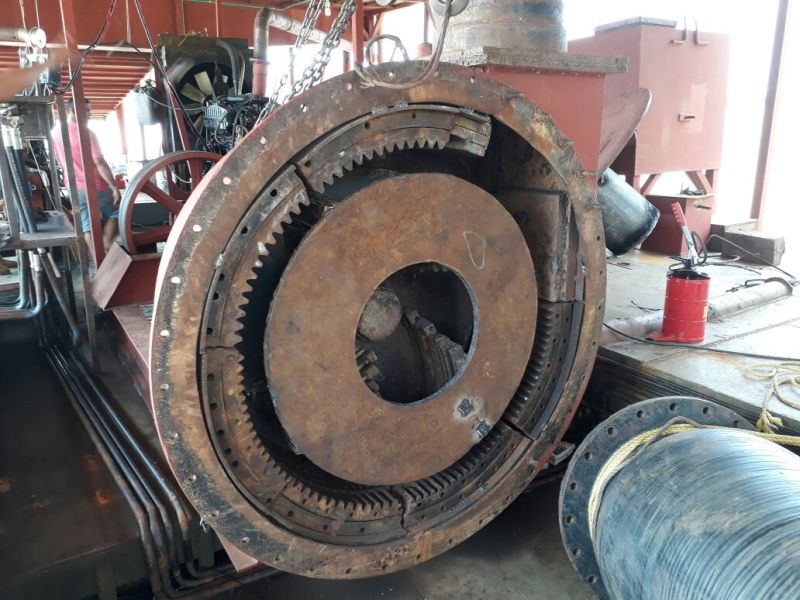
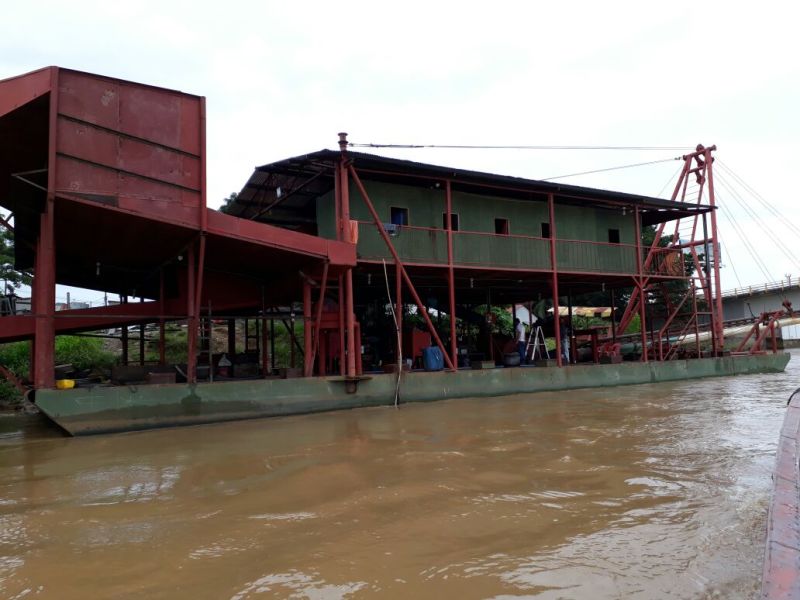
thanks in advance