Hey Guys, I have the case that I'm using 12mmØ bolt grade 4.6s/pb1230 for purlin connection cleats, what my concern is I have to use 6mm tolerance in steel connection plate, which is fine?
Also, the below hole values seems so high like 22mm dia hole for 12Ø bolt.. Please let me know your thoughts on this
Also the bolts should be galv or can be plain?
Thanks in advance!!
Also, the below hole values seems so high like 22mm dia hole for 12Ø bolt.. Please let me know your thoughts on this
Also the bolts should be galv or can be plain?
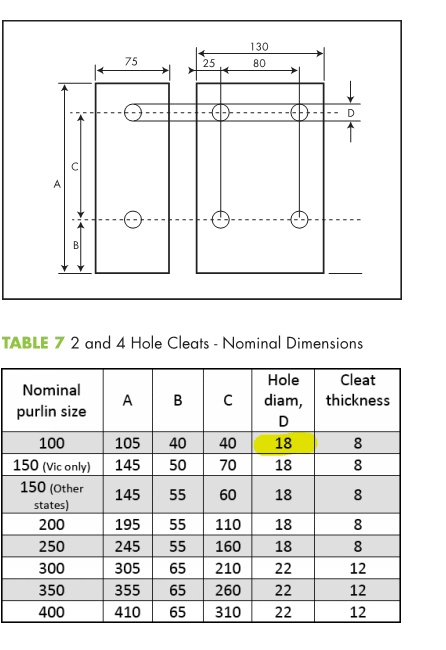
Thanks in advance!!