I received a "design" of a rib-spar joint from our design group (for whom the design inputs were received from client). The design contained staggered riveted joints. I was curious to learn about their choice of staggered instead of a usual in-line patterned riveted joint. Our design folks had no idea why such a choice was made and they carried out the design or its modifications just based on client's inputs. I tried to inquire internally but was told that we are in pure delivery mode & learning/research can be undertaken once the delivery is complete...a polite way of saying don't ask unnecessary questions, just do the task at hand.
Anyways, I have recreated the design as best as possible. Would the two rivets placed along the depth of the web provide any further additional support? As far as I could make out, there were no spacing issues or clashes, which would make staggered the preferred choice.
I also did a design of an in-line patterned riveted joint. Perhaps over the weekend, I will try to a FEM to see if there any benefits in using a staggered vs straight rivets pattern.
Anyways, I have recreated the design as best as possible. Would the two rivets placed along the depth of the web provide any further additional support? As far as I could make out, there were no spacing issues or clashes, which would make staggered the preferred choice.
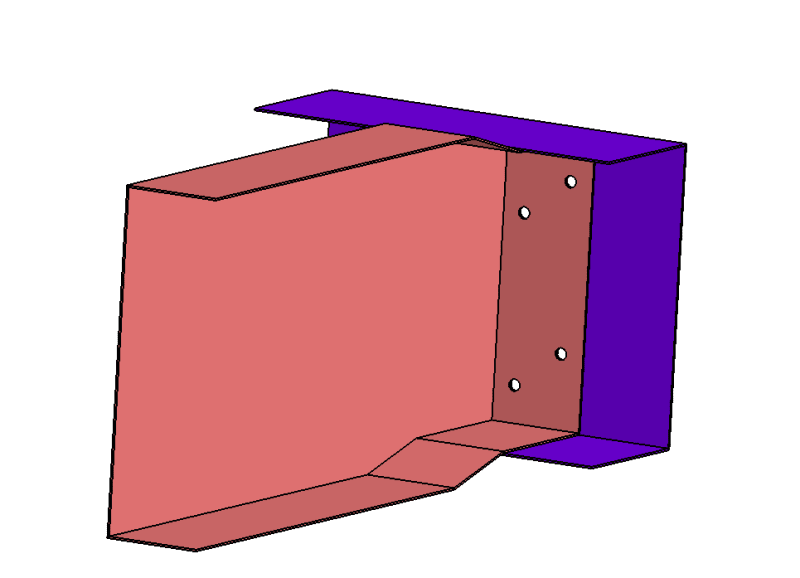
I also did a design of an in-line patterned riveted joint. Perhaps over the weekend, I will try to a FEM to see if there any benefits in using a staggered vs straight rivets pattern.
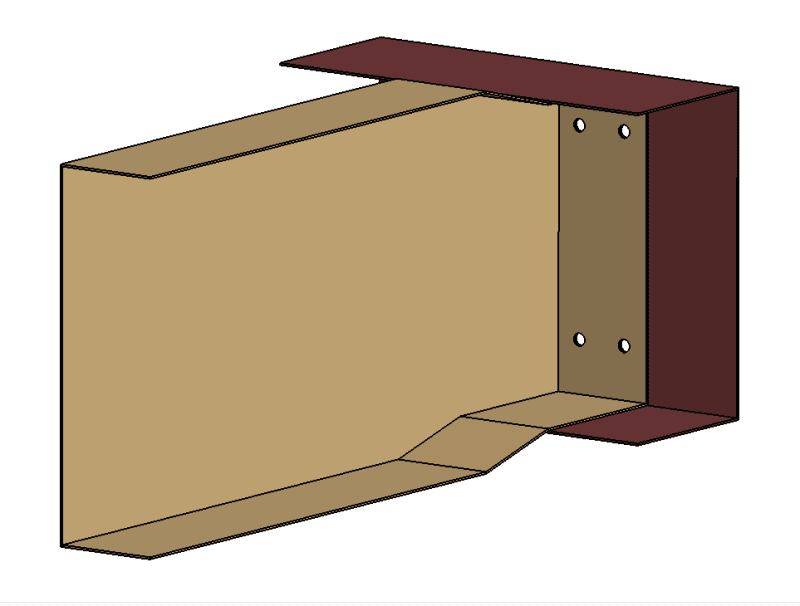