For this model I am simulating a simple long-gauge strain sensor mounted on the side of a beam under uniform tension.
The long-gauge sensor is a wire that is attached to L brackets on each end, which are fixed onto the surface of the beam
I am getting the following error: Too many attempts for this increment (1st increment)
Warnings:
For *tie pair (assembly__pickedsurf247-assembly__pickedsurf246), adjusted nodes with very small adjustments were not printed. Specify *preprint,model=yes for complete printout.
For *tie pair (assembly__pickedsurf248-assembly__pickedsurf220), adjusted nodes with very small adjustments were not printed. Specify *preprint,model=yes for complete printout.
Slave surface assembly__pickedset242_cns_ is a node-based surface used with surface to surface approach. In order to obtain improved stress accuracy with this approach, an element-based surface should be used instead.
Please make sure that the mesh density of the slave surface in the tie pair (assembly__pickedset242_cns_,assembly__pickedsurf241) is finer than the master surface. The analysis may run slower, may yield inaccurate results, and may require more memory if this is not the case.
For *tie pair (assembly__pickedset242_cns_-assembly__pickedsurf241), adjusted nodes with very small adjustments were not printed. Specify *preprint,model=yes for complete printout.
Slave surface assembly__pickedset244_cns_ is a node-based surface used with surface to surface approach. In order to obtain improved stress accuracy with this approach, an element-based surface should be used instead.
Please make sure that the mesh density of the slave surface in the tie pair (assembly__pickedset244_cns_,assembly__pickedsurf243) is finer than the master surface. The analysis may run slower, may yield inaccurate results, and may require more memory if this is not the case.
For *tie pair (assembly__pickedset244_cns_-assembly__pickedsurf243), adjusted nodes with very small adjustments were not printed. Specify *preprint,model=yes for complete printout.
Solver problem. Zero pivot when processing D.O.F. 1 of 2 nodes. The nodes have been identified in node set WarnNodeSolvProbZeroPiv_1_1_1_1_1.
Solver problem. Zero pivot when processing D.O.F. 2 of 9 nodes. The nodes have been identified in node set WarnNodeSolvProbZeroPiv_2_1_1_1_1.
Solver problem. Zero pivot when processing D.O.F. 1 of 2 nodes. The nodes have been identified in node set WarnNodeSolvProbZeroPiv_1_1_1_2_1.
Solver problem. Zero pivot when processing D.O.F. 1 of 4 nodes. The nodes have been identified in node set WarnNodeSolvProbZeroPiv_1_1_1_3_1.
Solver problem. Zero pivot when processing D.O.F. 3 of 1 nodes. The nodes have been identified in node set WarnNodeSolvProbZeroPiv_3_1_1_3_1.
Solver problem. Zero pivot when processing D.O.F. 1 of 6 nodes. The nodes have been identified in node set WarnNodeSolvProbZeroPiv_1_1_1_4_1.
Solver problem. Zero pivot when processing D.O.F. 3 of 4 nodes. The nodes have been identified in node set WarnNodeSolvProbZeroPiv_3_1_1_4_1.
Solver problem. Zero pivot when processing D.O.F. 1 of 8 nodes. The nodes have been identified in node set WarnNodeSolvProbZeroPiv_1_1_1_5_1.
Solver problem. Zero pivot when processing D.O.F. 2 of 5 nodes. The nodes have been identified in node set WarnNodeSolvProbZeroPiv_2_1_1_5_1.
Solver problem. Zero pivot when processing D.O.F. 3 of 8 nodes. The nodes have been identified in node set WarnNodeSolvProbZeroPiv_3_1_1_5_1.
=================================================================================
I have a feeling that this all has to do with the way the sensor and the L brackets are attached.
Right now I have the following interactions between my instances:
tie: wire fixed to the L brackets by tying the end node of the wire to the surface of the L bracket
tie: L bracket surface tied to the side surface of the beam.
I have been trying to adjust different things but nothing has worked so far, always the same set of warnings.
Have I missed something very obvious or?
Any advice would be super helpful! Thanks in advance!
The long-gauge sensor is a wire that is attached to L brackets on each end, which are fixed onto the surface of the beam
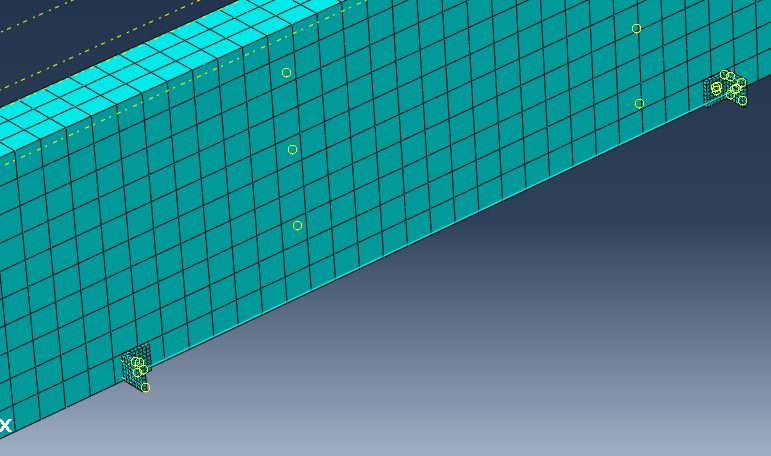
I am getting the following error: Too many attempts for this increment (1st increment)
Warnings:
For *tie pair (assembly__pickedsurf247-assembly__pickedsurf246), adjusted nodes with very small adjustments were not printed. Specify *preprint,model=yes for complete printout.
For *tie pair (assembly__pickedsurf248-assembly__pickedsurf220), adjusted nodes with very small adjustments were not printed. Specify *preprint,model=yes for complete printout.
Slave surface assembly__pickedset242_cns_ is a node-based surface used with surface to surface approach. In order to obtain improved stress accuracy with this approach, an element-based surface should be used instead.
Please make sure that the mesh density of the slave surface in the tie pair (assembly__pickedset242_cns_,assembly__pickedsurf241) is finer than the master surface. The analysis may run slower, may yield inaccurate results, and may require more memory if this is not the case.
For *tie pair (assembly__pickedset242_cns_-assembly__pickedsurf241), adjusted nodes with very small adjustments were not printed. Specify *preprint,model=yes for complete printout.
Slave surface assembly__pickedset244_cns_ is a node-based surface used with surface to surface approach. In order to obtain improved stress accuracy with this approach, an element-based surface should be used instead.
Please make sure that the mesh density of the slave surface in the tie pair (assembly__pickedset244_cns_,assembly__pickedsurf243) is finer than the master surface. The analysis may run slower, may yield inaccurate results, and may require more memory if this is not the case.
For *tie pair (assembly__pickedset244_cns_-assembly__pickedsurf243), adjusted nodes with very small adjustments were not printed. Specify *preprint,model=yes for complete printout.
Solver problem. Zero pivot when processing D.O.F. 1 of 2 nodes. The nodes have been identified in node set WarnNodeSolvProbZeroPiv_1_1_1_1_1.
Solver problem. Zero pivot when processing D.O.F. 2 of 9 nodes. The nodes have been identified in node set WarnNodeSolvProbZeroPiv_2_1_1_1_1.
Solver problem. Zero pivot when processing D.O.F. 1 of 2 nodes. The nodes have been identified in node set WarnNodeSolvProbZeroPiv_1_1_1_2_1.
Solver problem. Zero pivot when processing D.O.F. 1 of 4 nodes. The nodes have been identified in node set WarnNodeSolvProbZeroPiv_1_1_1_3_1.
Solver problem. Zero pivot when processing D.O.F. 3 of 1 nodes. The nodes have been identified in node set WarnNodeSolvProbZeroPiv_3_1_1_3_1.
Solver problem. Zero pivot when processing D.O.F. 1 of 6 nodes. The nodes have been identified in node set WarnNodeSolvProbZeroPiv_1_1_1_4_1.
Solver problem. Zero pivot when processing D.O.F. 3 of 4 nodes. The nodes have been identified in node set WarnNodeSolvProbZeroPiv_3_1_1_4_1.
Solver problem. Zero pivot when processing D.O.F. 1 of 8 nodes. The nodes have been identified in node set WarnNodeSolvProbZeroPiv_1_1_1_5_1.
Solver problem. Zero pivot when processing D.O.F. 2 of 5 nodes. The nodes have been identified in node set WarnNodeSolvProbZeroPiv_2_1_1_5_1.
Solver problem. Zero pivot when processing D.O.F. 3 of 8 nodes. The nodes have been identified in node set WarnNodeSolvProbZeroPiv_3_1_1_5_1.
=================================================================================
I have a feeling that this all has to do with the way the sensor and the L brackets are attached.
Right now I have the following interactions between my instances:
tie: wire fixed to the L brackets by tying the end node of the wire to the surface of the L bracket
tie: L bracket surface tied to the side surface of the beam.
I have been trying to adjust different things but nothing has worked so far, always the same set of warnings.
Have I missed something very obvious or?
Any advice would be super helpful! Thanks in advance!