NAFTALI-HAKOHEN
Civil/Environmental
am struggling to understand something,
in a simple truss with cross bracing like this:
why are the axial force compressions in the diagonal braces not equal when the structure is loaded with a unit horizontal force:
the horizontal reactions at supports are not equal as i would expect....
is it to do with the FE taking the unequal displacements ie unsymetrical displacement of upper beam?
thanks
in a simple truss with cross bracing like this:
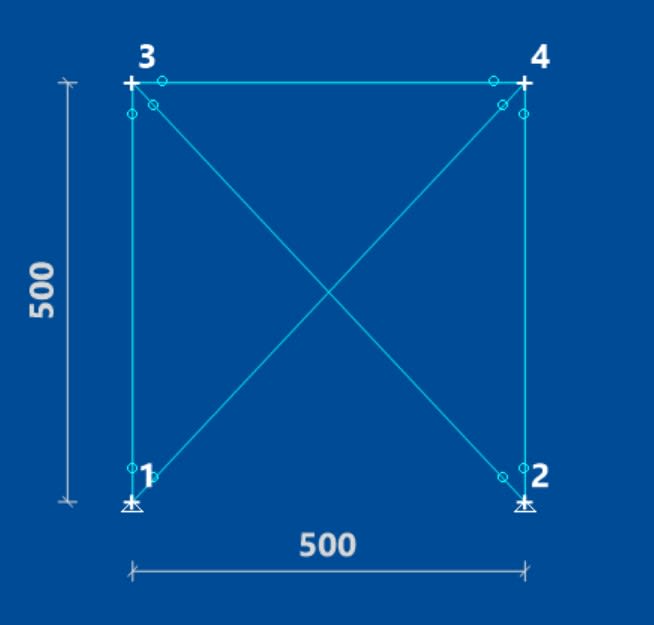
why are the axial force compressions in the diagonal braces not equal when the structure is loaded with a unit horizontal force:
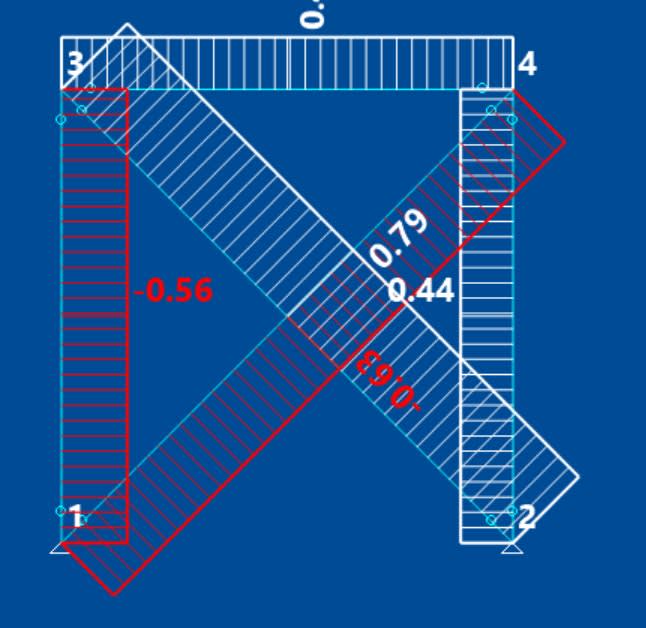
the horizontal reactions at supports are not equal as i would expect....
is it to do with the FE taking the unequal displacements ie unsymetrical displacement of upper beam?
thanks