phamENG
Structural
- Feb 6, 2015
- 7,600
In a gusset plate connection for a tension member in which the gusset is particularly long and/or narrow (typically a tapered gusset) can have what I have found in some literature to be called a "partial block shear" limit state. Intuitively, it makes sense. In traditional block shear, you have orthogonal shear rupture and tension yield or rupture planes and the block shear capacity is the sum of the strengths of those planes (per J4.3, AISC 360-10). But if the gusset tapers quickly, you could end up with an inclined failure plane from the bolts at the end of the tension member or weld to a point along the gusset (the inclined failure plane would be orthogonal to the free edge of the gusset rather than the line of force from the tension member).
Does anyone have any good, practical guidance on calculating the allowable strength in such a connection? The only real suggestion I've found in searching through literature online has been to apply the staggered bolt modification to net area from B4.3b (s2/4g), but they don't provide any evidence to back it up (theoretical justification or empirical results).
My thought is this: find the projected length of each leg of the partial shear failure on a line perpendicular to the line of force, and then determine a uniform linear distribution across each leg. Take that distribution and separate it back into the orthogonal components of the failure plane (shear and tension acting on that plane). Then, the equation from the manual would change to be something more like this: Rn=sum(0.60FuAnv)+sum(FuAnt). I'm not considering the tensile yield here as comparing the combined and then re-separated tension and shear stresses to different failure criteria seems flawed. This neglects relative stiffness of the various lines, but that seems ok as the size is relatively small and localized yielding to redistribute stresses is not altogether uncommon in these sorts of connections. A sketch is below - hopefully it helps to clarify.
Thanks. (For the record, I'm writing a spreadsheet to aide in the design and analysis of new or existing braced frame gusset connections, and I'm reviewing the various configurations I may consider or encounter...this is just one I haven't had to deal with much and would like to get some other opinions.)
Does anyone have any good, practical guidance on calculating the allowable strength in such a connection? The only real suggestion I've found in searching through literature online has been to apply the staggered bolt modification to net area from B4.3b (s2/4g), but they don't provide any evidence to back it up (theoretical justification or empirical results).
My thought is this: find the projected length of each leg of the partial shear failure on a line perpendicular to the line of force, and then determine a uniform linear distribution across each leg. Take that distribution and separate it back into the orthogonal components of the failure plane (shear and tension acting on that plane). Then, the equation from the manual would change to be something more like this: Rn=sum(0.60FuAnv)+sum(FuAnt). I'm not considering the tensile yield here as comparing the combined and then re-separated tension and shear stresses to different failure criteria seems flawed. This neglects relative stiffness of the various lines, but that seems ok as the size is relatively small and localized yielding to redistribute stresses is not altogether uncommon in these sorts of connections. A sketch is below - hopefully it helps to clarify.
Thanks. (For the record, I'm writing a spreadsheet to aide in the design and analysis of new or existing braced frame gusset connections, and I'm reviewing the various configurations I may consider or encounter...this is just one I haven't had to deal with much and would like to get some other opinions.)
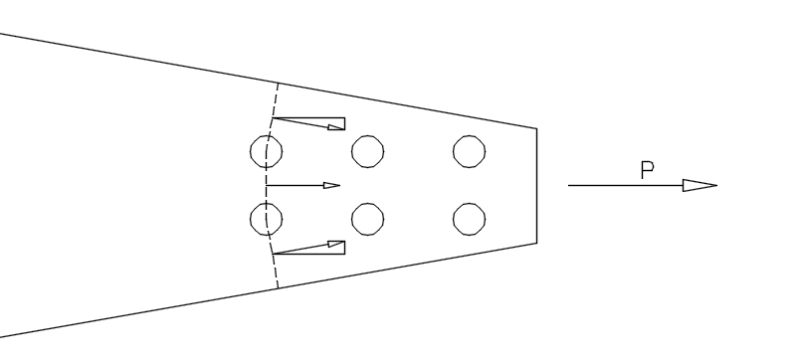