Hello all,
I am trying to model a dynamic model in Abaqus Explicit. It is an assembly made of multiple parts that begin moving from rest. It starts out fine, but as the parts' velocities begin to increase, the elements develop "waves", or distortion that looks like waves shown below. This eventually causes the simulation to abort. Does anyone have any clue why this may be happening?
Element Type: C3D8R
Hourglass Control: Enhanced
Contact Initialization: Treat as Interference Fit
Material Properties: Wood (E = 6.9e9 Pa)
Initially moving, there's no distortion:
Once it gets going, this happens:
Worth noting: The Explicit, Dynamic analysis is made from an assembly and a predefined field imported from an Standard, Static analysis using a python script.
I am trying to model a dynamic model in Abaqus Explicit. It is an assembly made of multiple parts that begin moving from rest. It starts out fine, but as the parts' velocities begin to increase, the elements develop "waves", or distortion that looks like waves shown below. This eventually causes the simulation to abort. Does anyone have any clue why this may be happening?
Element Type: C3D8R
Hourglass Control: Enhanced
Contact Initialization: Treat as Interference Fit
Material Properties: Wood (E = 6.9e9 Pa)
Initially moving, there's no distortion:
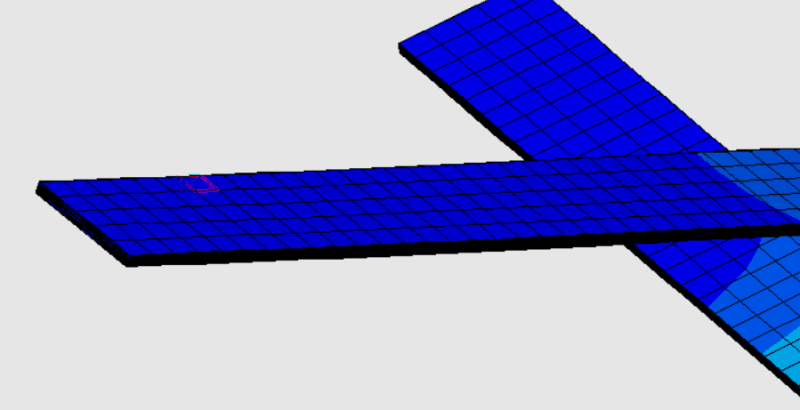
Once it gets going, this happens:
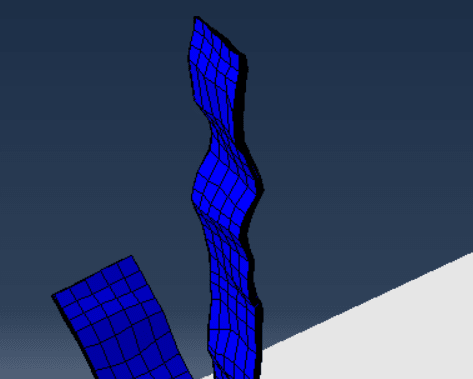
Worth noting: The Explicit, Dynamic analysis is made from an assembly and a predefined field imported from an Standard, Static analysis using a python script.