DAVIDSTECKER
Mechanical
thread330-184119
We have a very large casting in house (ASTM A757 Gr C1Q) that has Lab confirmed Aluminum Nitride Embrittlement.
The last post in the linked thread stated that Re-Austentizing could often remedy this condition.
My question is how reliable is this process.
The casting is mostly a cylinder; 31" ID X 6" Wall X 60" LTB.
The more we try to arc out crakes for repair the more the casting cracks.
We have been pre-heating the casting to at least 300F while air arcing.
Please let me know your thoughts and/or experience's regarding this condition.
Best regards, David
We have a very large casting in house (ASTM A757 Gr C1Q) that has Lab confirmed Aluminum Nitride Embrittlement.
The last post in the linked thread stated that Re-Austentizing could often remedy this condition.
My question is how reliable is this process.
The casting is mostly a cylinder; 31" ID X 6" Wall X 60" LTB.
The more we try to arc out crakes for repair the more the casting cracks.
We have been pre-heating the casting to at least 300F while air arcing.
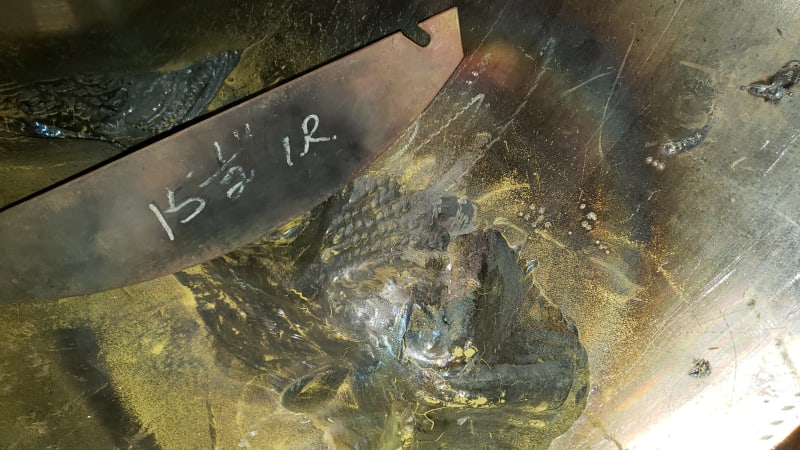
Please let me know your thoughts and/or experience's regarding this condition.
Best regards, David