I have to load test existing unbonded post-tensioning tendons to an existing buildings floor system that was built 50 years ago. I do this regularly - usually to 1/2" diameter 270 ksi 7-wire stranded tendons - but this one was built using 1/4" dia high-tensile wires with "upset" (button-heads) ends. An older, now antiquated PT system, that was once patented back in the 50's.
For this specific building, the tendon is made up of 12 individual wires connect to a circular 'washer' that bears on shims plates to a cast-in steel bearing plate. The 'washer' has a recess where a split-ring collar was attached and connected to a 70 ton stressing ram via a pull bar.
I have a (for me) unusual situation where I have get manufactured a custom lipped-and-threaded split-ring and a threaded collar as per the attached preliminary schematic:
Since the split ring is in two-pieces I will have an alignment pin/hole on each half so they marry-up, and also a nib (on top) that prevents the rings from turning when the collar in installed.
Previously I have had 4" diameter wedge collets manufactured (for a different project, but similar application) and they used a UNC thread that was tough to use in the field because of slight thread damage after use.
Is there a thread type (rolled, roped, square etc) that will work better in this application?
I only plan on getting two sets manufactured. I need to reuse the collar and rings several times, typically stressing to 100 kips.
Thanks in advance.
For this specific building, the tendon is made up of 12 individual wires connect to a circular 'washer' that bears on shims plates to a cast-in steel bearing plate. The 'washer' has a recess where a split-ring collar was attached and connected to a 70 ton stressing ram via a pull bar.
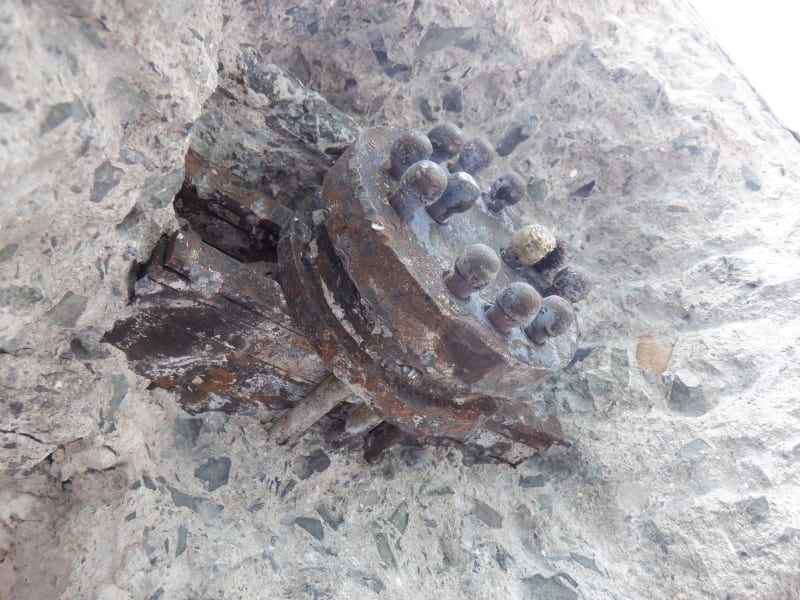
I have a (for me) unusual situation where I have get manufactured a custom lipped-and-threaded split-ring and a threaded collar as per the attached preliminary schematic:
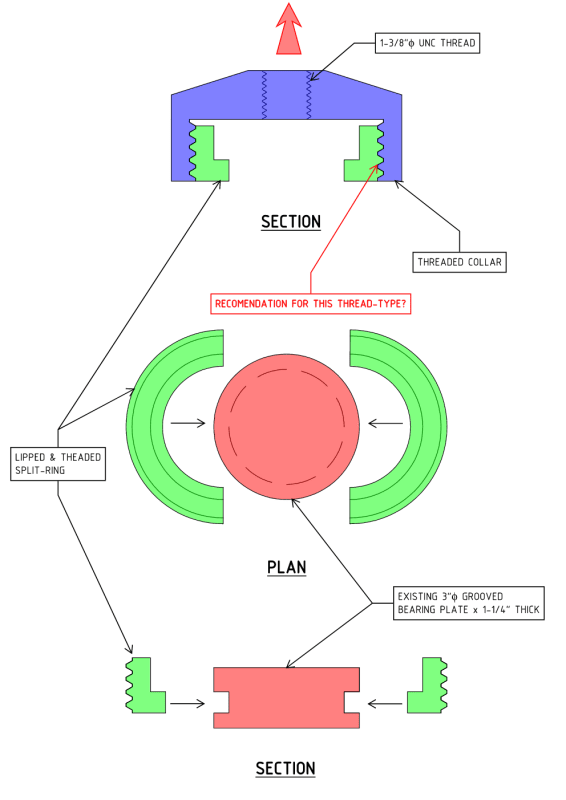
Since the split ring is in two-pieces I will have an alignment pin/hole on each half so they marry-up, and also a nib (on top) that prevents the rings from turning when the collar in installed.
Previously I have had 4" diameter wedge collets manufactured (for a different project, but similar application) and they used a UNC thread that was tough to use in the field because of slight thread damage after use.
Is there a thread type (rolled, roped, square etc) that will work better in this application?
I only plan on getting two sets manufactured. I need to reuse the collar and rings several times, typically stressing to 100 kips.
Thanks in advance.