amazing azza
Industrial
Hello friends,
We are about to start commissioning our HVAC system. However, I just noticed the following refrigerant piping connection that has been made at the outdoor/compressor unit.
Will the U-pocket not accumulate an oil plug? (Refrigerant is R407C). Also, does the filter-drier need isolation valves around it to facilitate changing it?
We are about to start commissioning our HVAC system. However, I just noticed the following refrigerant piping connection that has been made at the outdoor/compressor unit.
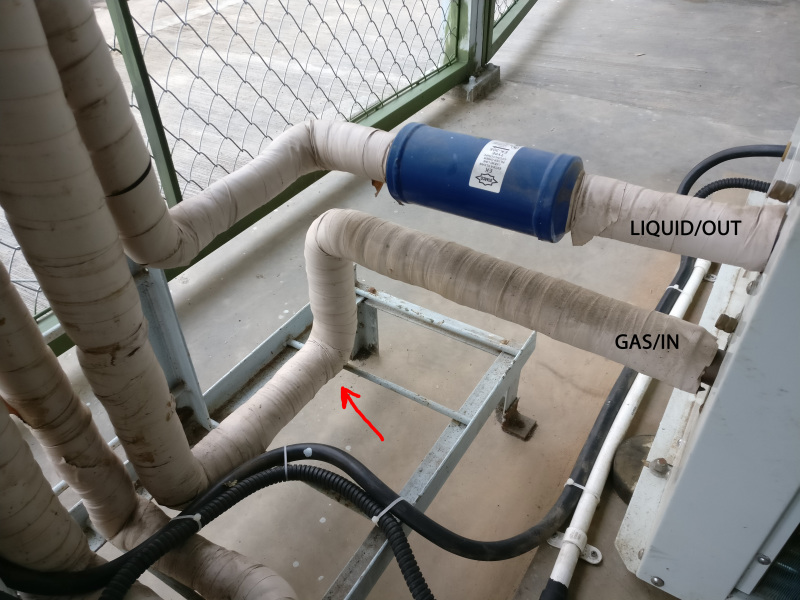
Will the U-pocket not accumulate an oil plug? (Refrigerant is R407C). Also, does the filter-drier need isolation valves around it to facilitate changing it?