Logan82
Structural
- May 5, 2021
- 212
Hi,
I have a situation where there is a rectangular hole in a beam. I am working on reinforcing the beam.
I have made sure that:
- The minimum bolt edge distance is respected.
- The minimum bolt pitch is respected.
- The bolt resistance is sufficient to resist the point load.
- The bearing resistance of the steel beam bolt holes are sufficient to resist the point load.
- The reinforcing plate is more thick and has a higher Fy and Fu than the web of the beam.
- There are 2 reinforcing plates on each side of the web, so it is symmetrical.
Is there anything else I should consider?
I have a situation where there is a rectangular hole in a beam. I am working on reinforcing the beam.
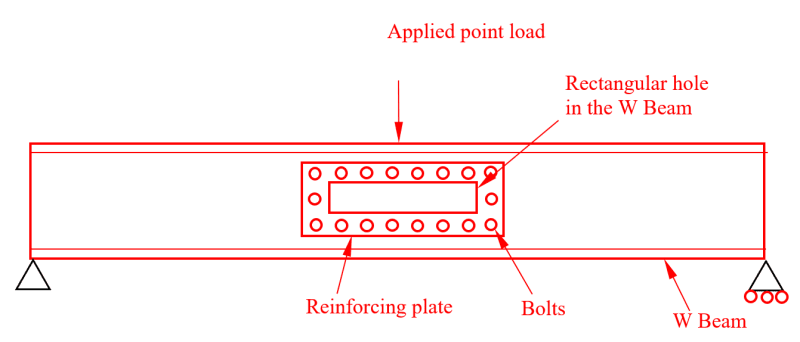
I have made sure that:
- The minimum bolt edge distance is respected.
- The minimum bolt pitch is respected.
- The bolt resistance is sufficient to resist the point load.
- The bearing resistance of the steel beam bolt holes are sufficient to resist the point load.
- The reinforcing plate is more thick and has a higher Fy and Fu than the web of the beam.
- There are 2 reinforcing plates on each side of the web, so it is symmetrical.
Is there anything else I should consider?