Hello,
I am trying to simplify a cutting process (milling) in which there is a disturbed uniform force in Z-direction acting on a workpiece (representing my tool force), moving from point A to B in a straight line in X-direction. Instead of dealing with subroutines such as DLOAD and VLOAD, I have decided to simulate it in some increments. I have attached the image of my work below.
The workpiece is clamped at the corners to four location pins (U1=U2=U3=UR1=UR2=UR3=0).
My question is, how can I practically do such a thing with ABAQUS? I'm new to ABAQUS and I know how check the "Element Deletion" box in "Element Type" window. (is this better to be done in Implicit or Explicit?)
Thank you in advance.
I am trying to simplify a cutting process (milling) in which there is a disturbed uniform force in Z-direction acting on a workpiece (representing my tool force), moving from point A to B in a straight line in X-direction. Instead of dealing with subroutines such as DLOAD and VLOAD, I have decided to simulate it in some increments. I have attached the image of my work below.
The workpiece is clamped at the corners to four location pins (U1=U2=U3=UR1=UR2=UR3=0).
My question is, how can I practically do such a thing with ABAQUS? I'm new to ABAQUS and I know how check the "Element Deletion" box in "Element Type" window. (is this better to be done in Implicit or Explicit?)
Thank you in advance.
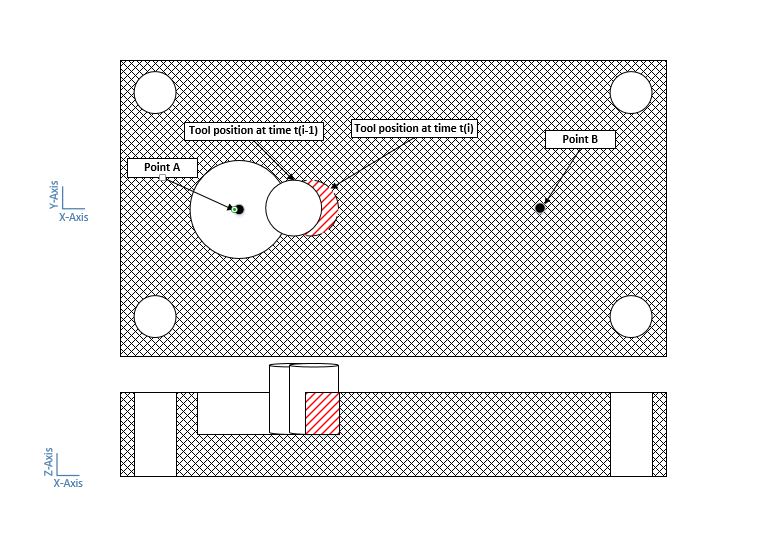
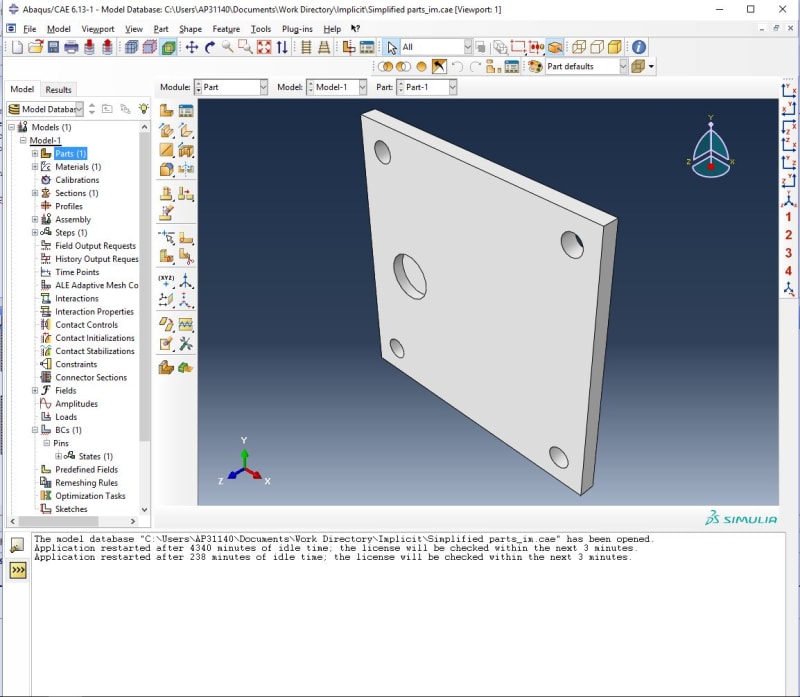