Hello, can anyone guide me in the right direction here.
I am working on a project where the building is facing the beach and the garage slab (post-tension), is cracked and some areas have a delaminating portion Of concrete completely fallen and leaving the tendon exposed.this area is the edge of the slab facing the beach, which was caused by corrosion
See pictures..
I am to provide a repair plan for the slab.
Please mention any reference in the code that can be useful or good tips from your experience.
I have worked on column and beam repair previously but never a post-tension slav, which I know it is a different ball-game.
Also any ideas what are the tiny holes in the slab? Any purpose?
I am working on a project where the building is facing the beach and the garage slab (post-tension), is cracked and some areas have a delaminating portion Of concrete completely fallen and leaving the tendon exposed.this area is the edge of the slab facing the beach, which was caused by corrosion
See pictures..
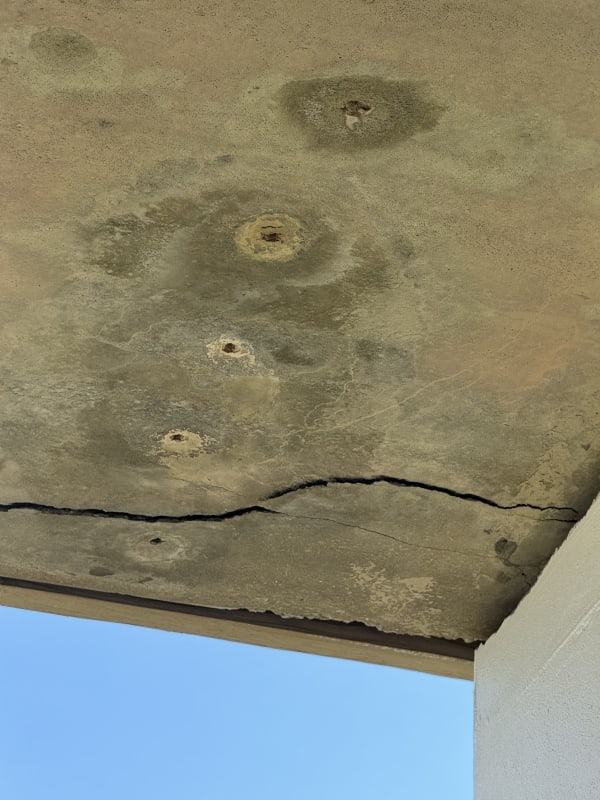
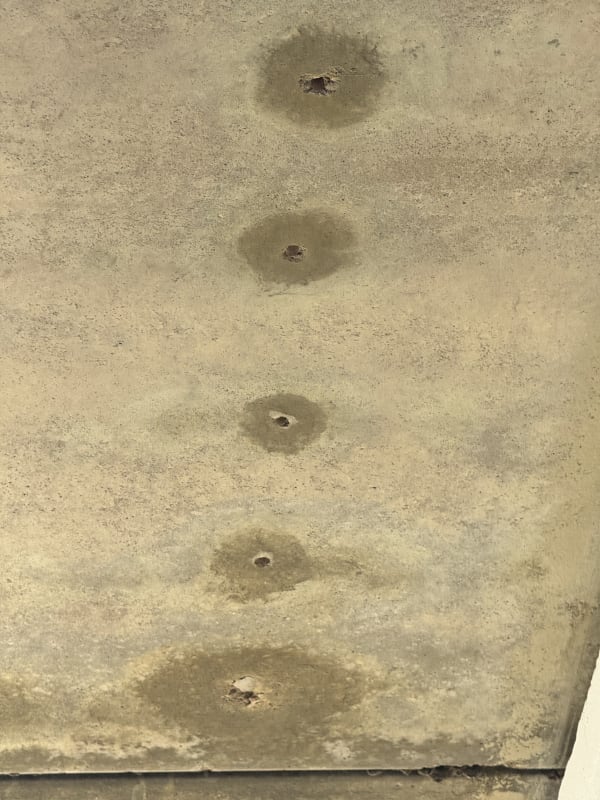
I am to provide a repair plan for the slab.
Please mention any reference in the code that can be useful or good tips from your experience.
I have worked on column and beam repair previously but never a post-tension slav, which I know it is a different ball-game.
Also any ideas what are the tiny holes in the slab? Any purpose?