Azzazil
Automotive
- Feb 1, 2020
- 98
I have same part in two different assemblies with different shape. Since when I create any 3DPart by our PML system I get to him attached unique ID Part Name, and any additional creation of 3DPart will create new ID Part Name so in this case I can't store geometry of other shape configuration under different 3DPart since when I create BoM it will generate 2 different ERP codes that will be in system for same part.
To explain more in details here is sketch.
In sketch you can see red line which represents my part with developed length, other part is marked with blue line and it represents my part in first configuration and green line represents my part in second configuration.
Does anybody have idea how to solve this since I design in 3Dx which allows creation of 3DShape object, I place in 3DShape surfaces of two configurations and instantiate my part in both sub-assemblies with original ID Part Name, but I am not sure if this approach is best.
To explain more in details here is sketch.
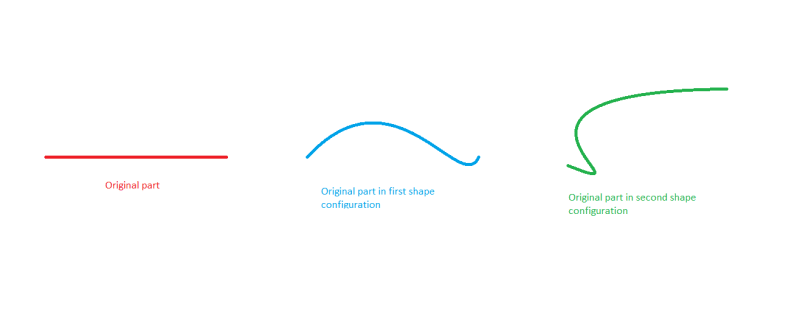
In sketch you can see red line which represents my part with developed length, other part is marked with blue line and it represents my part in first configuration and green line represents my part in second configuration.
Does anybody have idea how to solve this since I design in 3Dx which allows creation of 3DShape object, I place in 3DShape surfaces of two configurations and instantiate my part in both sub-assemblies with original ID Part Name, but I am not sure if this approach is best.