Vlaude
Geotechnical
- Jul 1, 2015
- 3
I am curious to get comments on the foundation design provided. 80% of the home builders in the area are constructing a stemwall foundation and 15% are post-tension, with a few other variations. I am looking at beefing up the footings (they are well below the frost line - in the south) and pouring the slab on the footing in a monolithic pour vs two pours as many stemwalls are poured.
This will be a single story home with #4 rebar on 28" with exception to the toe downs/beams where is will be much closer. Plan on doweling in the toe down in the slab to the footing. There will be footings at load points and thickened beams across all load bearing walls. Concrete will be 4,000 PSI no fiber mesh and soils bearing capacity I'm guessing is not great, around 2,000. I will confirm with a geotech. Just curious on general comments... Thanks!
This will be a single story home with #4 rebar on 28" with exception to the toe downs/beams where is will be much closer. Plan on doweling in the toe down in the slab to the footing. There will be footings at load points and thickened beams across all load bearing walls. Concrete will be 4,000 PSI no fiber mesh and soils bearing capacity I'm guessing is not great, around 2,000. I will confirm with a geotech. Just curious on general comments... Thanks!
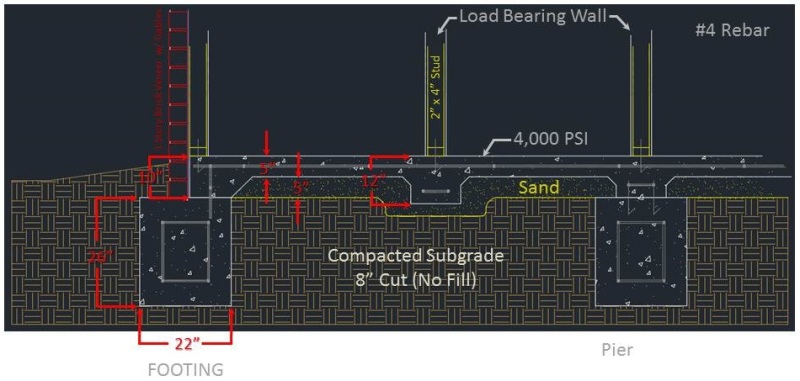