I have a project of designing a retaining wall, but there is a 20" thick layer of peat in the soil right underneath. Below that there is water table. I see that peat can take an allowable pressure of 1,500 psf. The rest of the soil is a good solid 3 tons per square foot capacity. I wonder if 20 inches is something worth worrying about or if I should just recommend that we dig out all that peat, replace it with infill and build the retaining wall. I fear that anything else is going to make this much more expensive. Any ideas on this matter?
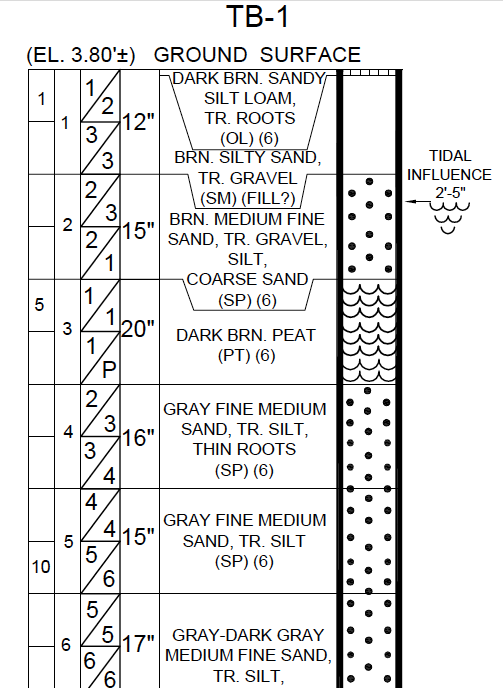