Hi all,
Currently going through the design of the glazed roof system, as shown below.
In particular, I'm having a good look at the connection of the cantilevered/tapered "T" member (multi-coloured 380BT) coming into the main beam(grey 400x300x8.0 RHS).
I would like to check the capacity of the RHS side wall if I were to directly weld the "T" member. Note I've used the plastic section modulus for the RHS side wall.
My design philosophy so far: Would be great if anybody could provide some feedback on my philosophy and/or ideas about this connection.
Currently going through the design of the glazed roof system, as shown below.
In particular, I'm having a good look at the connection of the cantilevered/tapered "T" member (multi-coloured 380BT) coming into the main beam(grey 400x300x8.0 RHS).
I would like to check the capacity of the RHS side wall if I were to directly weld the "T" member. Note I've used the plastic section modulus for the RHS side wall.
My design philosophy so far: Would be great if anybody could provide some feedback on my philosophy and/or ideas about this connection.
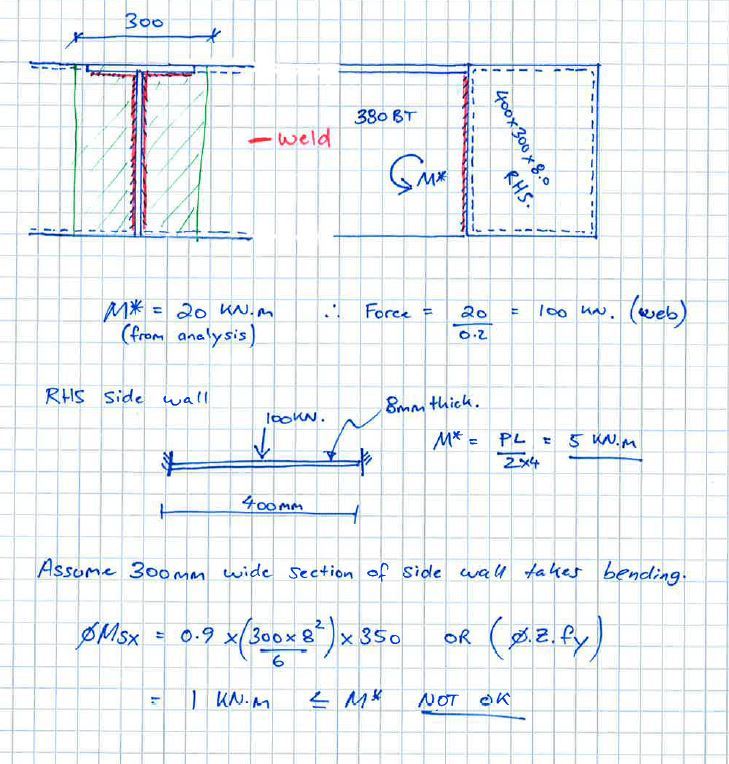
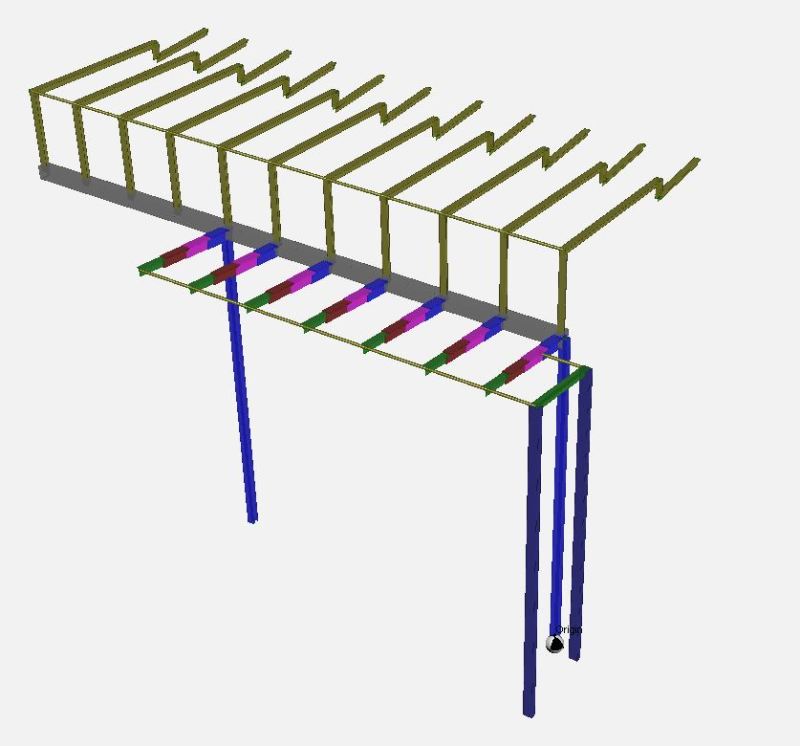