I have developed the rolling process in 2D.
The slab's geometry before the rolling was:
-length: 120 milimeters
-height: 2 milimeter
After the rolling process:
-length: 120 milimeters
-height: 0.9 milimeter
Relative displacement in 1 direction: 8.82149e-005 milimeters
Why there is no increase in strip's length? It is very weird. I do not understand it. Some of the material disappeared, or what?
The slab's geometry before the rolling was:
-length: 120 milimeters
-height: 2 milimeter
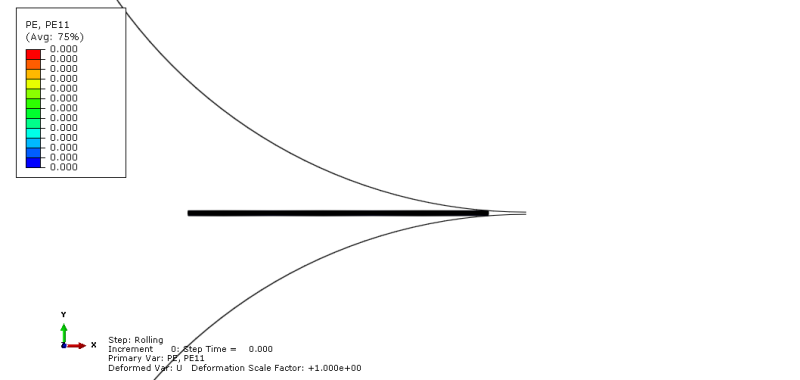
After the rolling process:
-length: 120 milimeters
-height: 0.9 milimeter
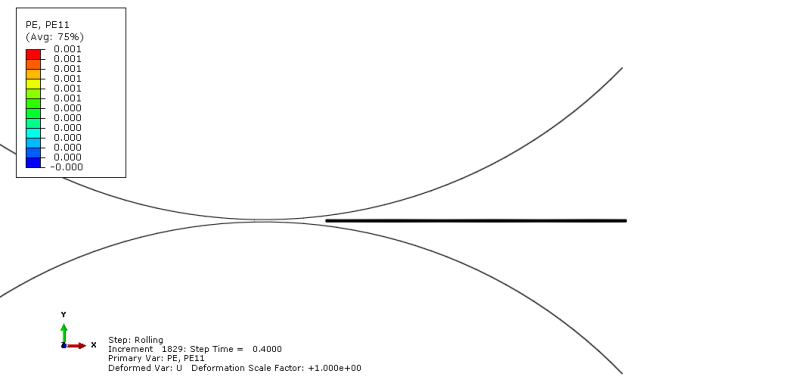
Relative displacement in 1 direction: 8.82149e-005 milimeters
Why there is no increase in strip's length? It is very weird. I do not understand it. Some of the material disappeared, or what?