Hello,
I am wondering if there is a way to utilize wood trusses like in the picture below. The owners do not want ceiling joists and for the sake of the discussion, let's say that a ridge beam is not an option (the span would be over 35 feet). I am worried about the thrust, as once I tie the trusses down to the walls it will create a horizontal pin at each wall. Does anyone have a suggestion on what to do in such a situation? Maybe a bracket that allows for lateral movement?
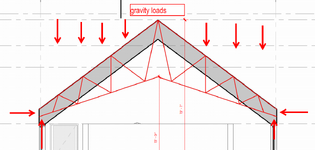
I am wondering if there is a way to utilize wood trusses like in the picture below. The owners do not want ceiling joists and for the sake of the discussion, let's say that a ridge beam is not an option (the span would be over 35 feet). I am worried about the thrust, as once I tie the trusses down to the walls it will create a horizontal pin at each wall. Does anyone have a suggestion on what to do in such a situation? Maybe a bracket that allows for lateral movement?
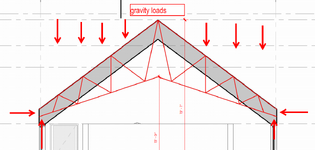