EngDM
Structural
- Aug 10, 2021
- 564
Hey all,
I've got a connection to an HSS pipe that I'm trying to analyze but not really sure where to start.
Picture a 4"Ø pipe being supported by a channel, where the pipe is in contact with the flanges of the channel, almost like it's sitting in it. There is a lateral force perpendicular to the pipe, so the channel flanges will push towards the pipe wall. Channel will be welded to the pipe on the flanges, either a fillet or perhaps a prep'd edge to make sure my fusion face is wide enough on the channel.
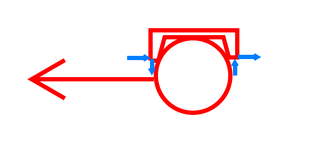
Other than the K2.1 HSS plastification check, I'm not sure what else I should consider.
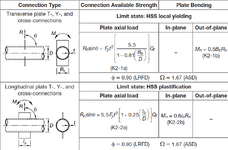
One concern I have regarding the K2.1 equations, is that the plate in my case would not be about the pipe central axis', but rather 1/3 from the top edge approximately. Since the load from the pipe is from the centroid, I will need to resolve a moment as well as the shear loads (reactions shown in blue in my sketch above); this behaviour isn't explicitely covered by K2.1.
I've got a connection to an HSS pipe that I'm trying to analyze but not really sure where to start.
Picture a 4"Ø pipe being supported by a channel, where the pipe is in contact with the flanges of the channel, almost like it's sitting in it. There is a lateral force perpendicular to the pipe, so the channel flanges will push towards the pipe wall. Channel will be welded to the pipe on the flanges, either a fillet or perhaps a prep'd edge to make sure my fusion face is wide enough on the channel.
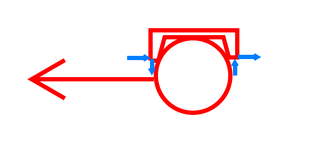
Other than the K2.1 HSS plastification check, I'm not sure what else I should consider.
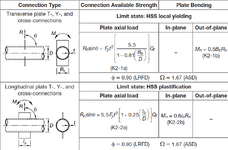
One concern I have regarding the K2.1 equations, is that the plate in my case would not be about the pipe central axis', but rather 1/3 from the top edge approximately. Since the load from the pipe is from the centroid, I will need to resolve a moment as well as the shear loads (reactions shown in blue in my sketch above); this behaviour isn't explicitely covered by K2.1.