Greetings
I want to simulate scratch in ABAQUS I define it in three steps: indenting (load control), displacement (maintaining the load from the first step), and the unloading. however, when my model goes to the second step which is scratching, my contact broke off and the rigid analytical body goes up (figure 1), also for the third step the rigid body comes back to its origin. I would really appreciate it if you can tell me what might be the problem. below are my boundary constraints and interaction.
i define the interaction as node to surface small sliding (for finite sliding there is no contact loss but it cannot understand that i introduce friction)
Step 1 is load control and then step displacement in Z direction, and then with displacement control should goes up.
** INTERACTION PROPERTIES
**
*Surface Interaction, name=_Int-1-Prop
1.,
*Friction
0.,
*Surface Behavior, pressure-overclosure=HARD
*Surface Interaction, name=indent
1.,
*Friction
0.,
*Surface Behavior, pressure-overclosure=HARD
*Surface Interaction, name=scratch
1.,
*Friction, slip tolerance=0.005
0.1,
*Surface Behavior, pressure-overclosure=HARD
**
** BOUNDARY CONDITIONS
**
** Name: but Type: Displacement/Rotation
*Boundary
but, 1, 1
but, 2, 2
but, 3, 3
** Name: sym Type: Displacement/Rotation
*Boundary
Set-7, 1, 1
Set-7, 5, 5
Set-7, 6, 6
**
** INTERACTIONS
**
** Interaction: Int-1
*Contact Pair, interaction=_Int-1-Prop, small sliding
Part-1-1.Surf-1, Part-2-1.Surf-1
** ----------------------------------------------------------------
**
** STEP: Step-1
**
*Step, name=Step-1, nlgeom=YES, inc=1000
*Static
0.0001, 1., 1e-09, 1.
**
** BOUNDARY CONDITIONS
**
** Name: control refrence point Type: Displacement/Rotation
*Boundary
Set-4, 1, 1
Set-4, 3, 3
Set-4, 4, 4
Set-4, 5, 5
Set-4, 6, 6
**
** LOADS
**
** Name: Load-1 Type: Concentrated force
*Cload
Set-4, 2, -100000.
**
** ----------------------------------------------------------------
**
** STEP: Step-2
**
*Step, name=Step-2, nlgeom=YES, inc=1000
*Static
0.0001, 1., 1e-09, 1.
**
** BOUNDARY CONDITIONS
**
** Name: control refrence point Type: Displacement/Rotation
*Boundary
Set-4, 3, 3, -400.
**
** INTERACTIONS
**
** Interaction: Int-1
*Change Friction, interaction=_Int-1-Prop
*Friction, slip tolerance=0.005
0.1,
**
** ----------------------------------------------------------------
**
** STEP: Step-3
**
*Step, name=Step-3, nlgeom=YES, inc=1000
*Static
0.01, 1., 1e-08, 1.
**
** BOUNDARY CONDITIONS
**
** Name: control refrence point Type: Displacement/Rotation
*Boundary
Set-4, 2, 2
Set-4, 3, 3
**
** LOADS
**
** Name: Load-1 Type: Concentrated force
*Cload
Set-4, 2, 0.
**
** INTERACTIONS
**
** Interaction: Int-1
*Change Friction, interaction=_Int-1-Prop
*Friction
0.,
**
I want to simulate scratch in ABAQUS I define it in three steps: indenting (load control), displacement (maintaining the load from the first step), and the unloading. however, when my model goes to the second step which is scratching, my contact broke off and the rigid analytical body goes up (figure 1), also for the third step the rigid body comes back to its origin. I would really appreciate it if you can tell me what might be the problem. below are my boundary constraints and interaction.
i define the interaction as node to surface small sliding (for finite sliding there is no contact loss but it cannot understand that i introduce friction)
Step 1 is load control and then step displacement in Z direction, and then with displacement control should goes up.
** INTERACTION PROPERTIES
**
*Surface Interaction, name=_Int-1-Prop
1.,
*Friction
0.,
*Surface Behavior, pressure-overclosure=HARD
*Surface Interaction, name=indent
1.,
*Friction
0.,
*Surface Behavior, pressure-overclosure=HARD
*Surface Interaction, name=scratch
1.,
*Friction, slip tolerance=0.005
0.1,
*Surface Behavior, pressure-overclosure=HARD
**
** BOUNDARY CONDITIONS
**
** Name: but Type: Displacement/Rotation
*Boundary
but, 1, 1
but, 2, 2
but, 3, 3
** Name: sym Type: Displacement/Rotation
*Boundary
Set-7, 1, 1
Set-7, 5, 5
Set-7, 6, 6
**
** INTERACTIONS
**
** Interaction: Int-1
*Contact Pair, interaction=_Int-1-Prop, small sliding
Part-1-1.Surf-1, Part-2-1.Surf-1
** ----------------------------------------------------------------
**
** STEP: Step-1
**
*Step, name=Step-1, nlgeom=YES, inc=1000
*Static
0.0001, 1., 1e-09, 1.
**
** BOUNDARY CONDITIONS
**
** Name: control refrence point Type: Displacement/Rotation
*Boundary
Set-4, 1, 1
Set-4, 3, 3
Set-4, 4, 4
Set-4, 5, 5
Set-4, 6, 6
**
** LOADS
**
** Name: Load-1 Type: Concentrated force
*Cload
Set-4, 2, -100000.
**
** ----------------------------------------------------------------
**
** STEP: Step-2
**
*Step, name=Step-2, nlgeom=YES, inc=1000
*Static
0.0001, 1., 1e-09, 1.
**
** BOUNDARY CONDITIONS
**
** Name: control refrence point Type: Displacement/Rotation
*Boundary
Set-4, 3, 3, -400.
**
** INTERACTIONS
**
** Interaction: Int-1
*Change Friction, interaction=_Int-1-Prop
*Friction, slip tolerance=0.005
0.1,
**
** ----------------------------------------------------------------
**
** STEP: Step-3
**
*Step, name=Step-3, nlgeom=YES, inc=1000
*Static
0.01, 1., 1e-08, 1.
**
** BOUNDARY CONDITIONS
**
** Name: control refrence point Type: Displacement/Rotation
*Boundary
Set-4, 2, 2
Set-4, 3, 3
**
** LOADS
**
** Name: Load-1 Type: Concentrated force
*Cload
Set-4, 2, 0.
**
** INTERACTIONS
**
** Interaction: Int-1
*Change Friction, interaction=_Int-1-Prop
*Friction
0.,
**
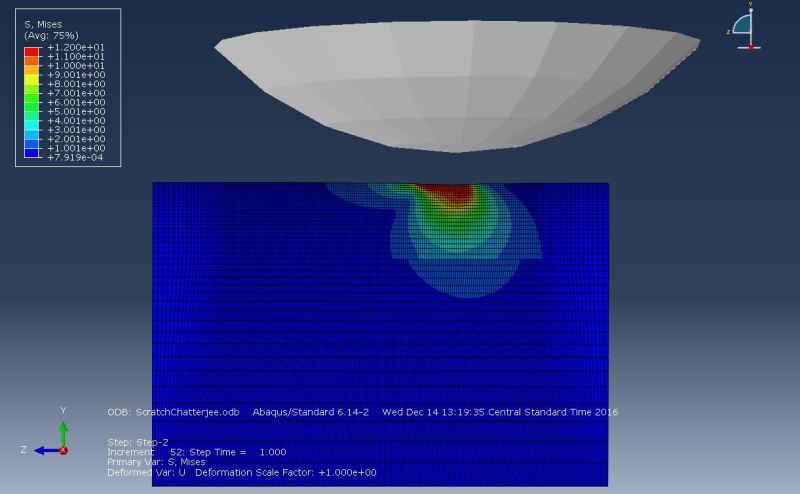
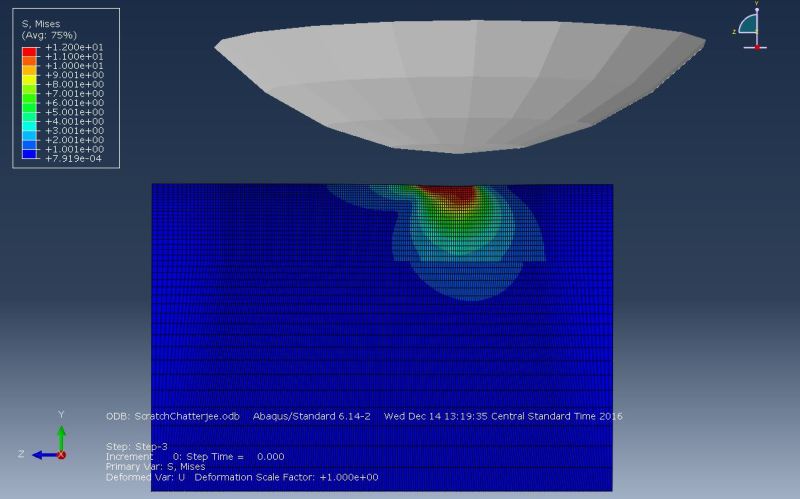
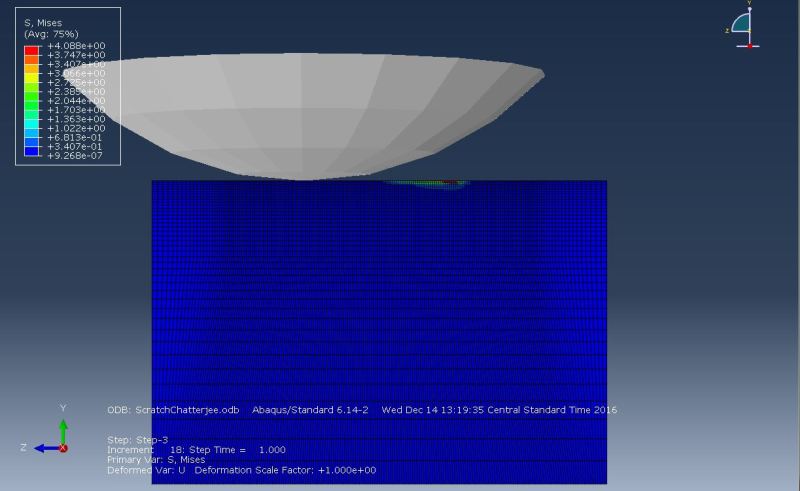