PrintScaffold
Mechanical
Hello everyone!
I wonder if formulas exist to analytically draw the shape of the gear tooth fillet (the same way as with the involute shape of the main part of the tooth itself)? I understand that it is being formed by the hob, and essentially is the product of the relative motion of the hob and wheel itself. Is it possible to express this shape by an equation?
I wonder if formulas exist to analytically draw the shape of the gear tooth fillet (the same way as with the involute shape of the main part of the tooth itself)? I understand that it is being formed by the hob, and essentially is the product of the relative motion of the hob and wheel itself. Is it possible to express this shape by an equation?
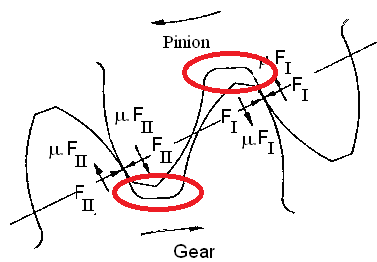