TomoB
Mechanical
- Dec 15, 2021
- 18
Hello,
I need to check the shear lugs (axial stoppers) on pipelines with respect to the loads that were calculated in the stress analysis. I came across a project where Finite Element Analysis was used for these components. But is this really necessary?
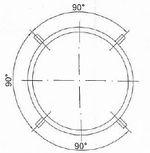
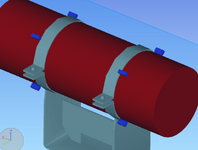
What is your approach? Do you rely on hand calculations, and if so, which methods or standards do you use? Are there specific procedures or rules of thumb that you follow for designing these components?
Thank you for your time!
I need to check the shear lugs (axial stoppers) on pipelines with respect to the loads that were calculated in the stress analysis. I came across a project where Finite Element Analysis was used for these components. But is this really necessary?

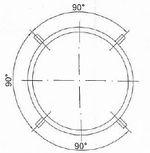
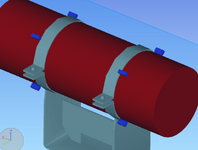
What is your approach? Do you rely on hand calculations, and if so, which methods or standards do you use? Are there specific procedures or rules of thumb that you follow for designing these components?
Thank you for your time!