Hello,
I would like to please check how difficult might be the manufacture of the suggested design below.
I am sure there are more options of manufacturing this, but I am interested to know if the suggested design is OK.
Here is a picture of the stainless steel 304L or 316L (both possible) 2.5 mm bended box, while dimensions are in [mm]:
The design intent is creating this with minimum weldment lines.
Here is a picture of the box with the bended lines marked on it with red dashed lines:
Here is a flattened configuration of this box while the bended lines are marked with red dashed lines:
Now I am going to present the (mine) suggested steps for creating this box.
1st step - bending these lines:
2nd step - bending this line:
3rd step - bending these lines:
4th step - bending this line:
5th step - bending this line:
6th step - bending this line:
7th step - bending this line:
I would like to please check how difficult might be the manufacture of the suggested design below.
I am sure there are more options of manufacturing this, but I am interested to know if the suggested design is OK.
Here is a picture of the stainless steel 304L or 316L (both possible) 2.5 mm bended box, while dimensions are in [mm]:
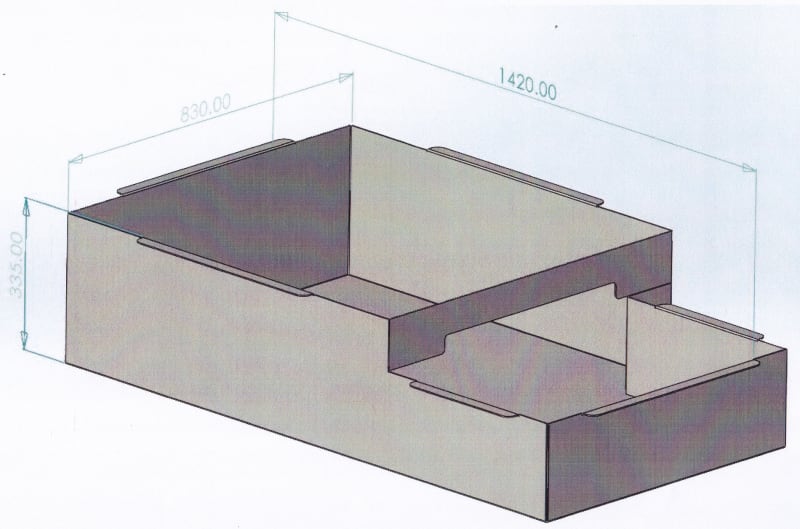
The design intent is creating this with minimum weldment lines.
Here is a picture of the box with the bended lines marked on it with red dashed lines:
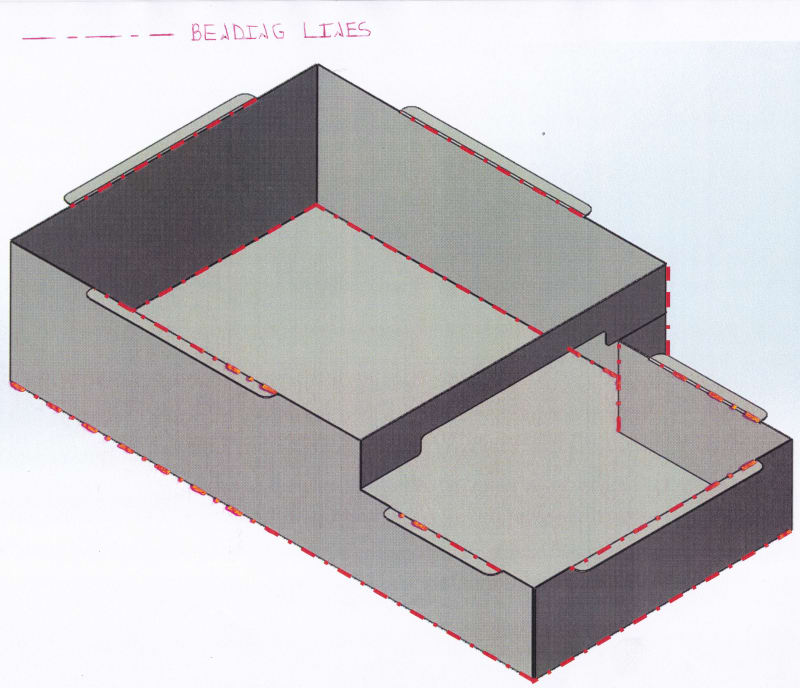
Here is a flattened configuration of this box while the bended lines are marked with red dashed lines:
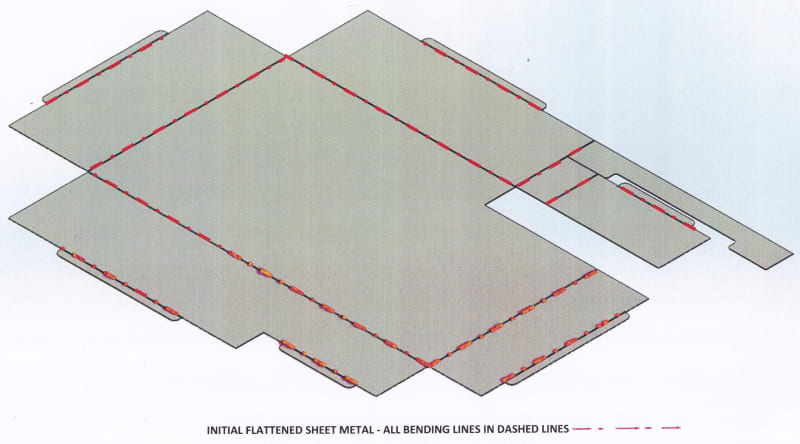
Now I am going to present the (mine) suggested steps for creating this box.
1st step - bending these lines:
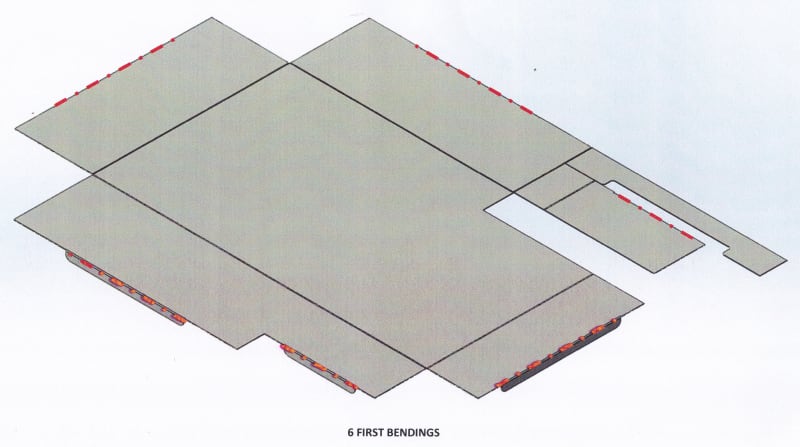
2nd step - bending this line:
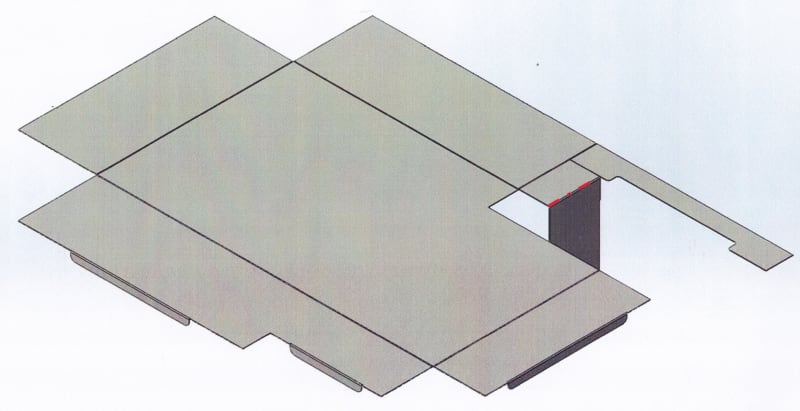
3rd step - bending these lines:
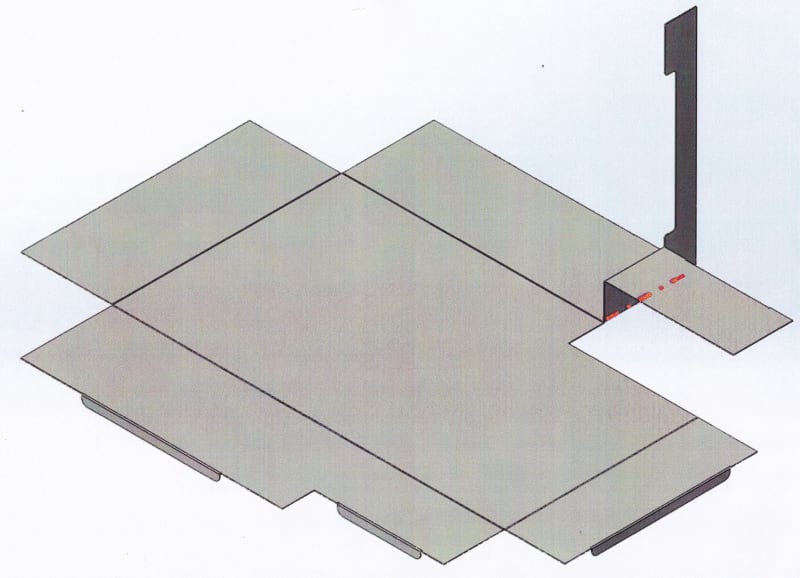
4th step - bending this line:
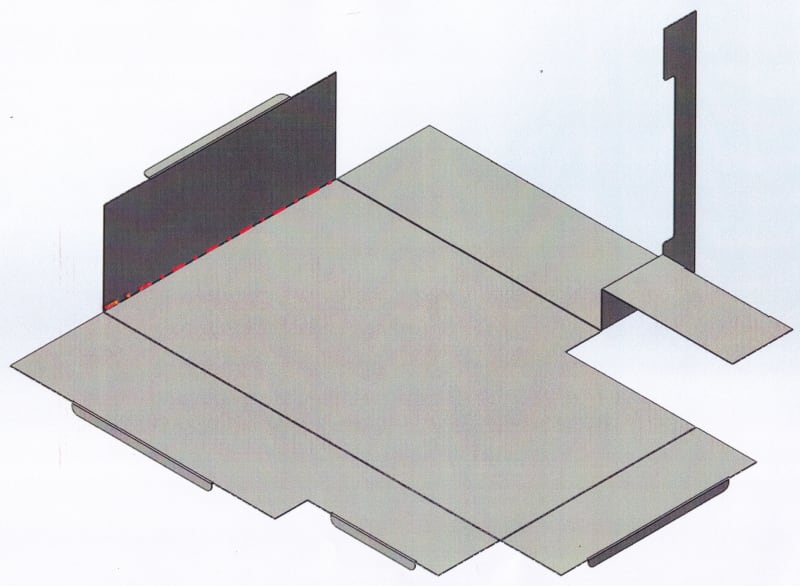
5th step - bending this line:
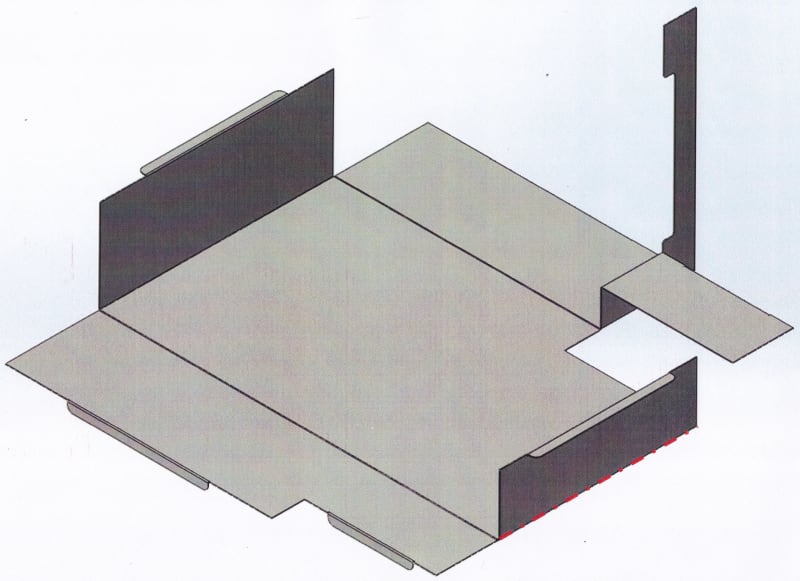
6th step - bending this line:
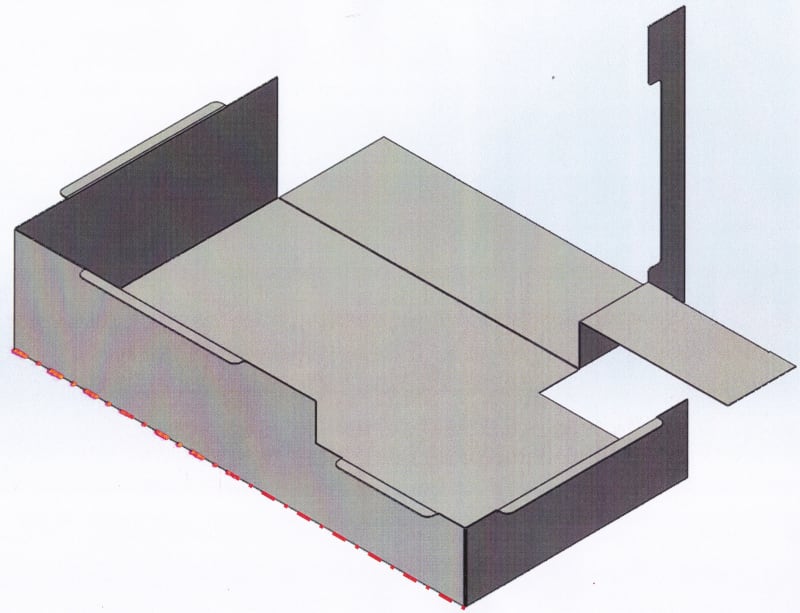
7th step - bending this line:
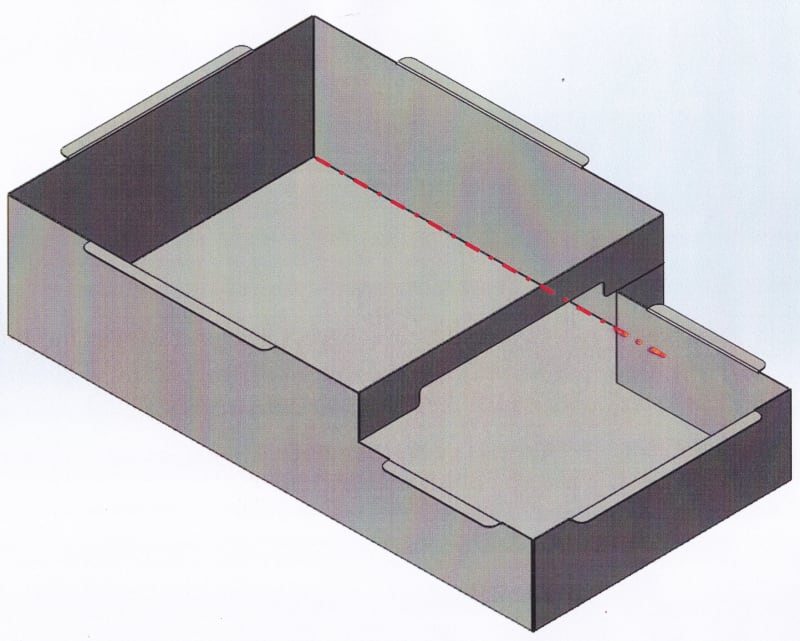