I'm trying to figure out how embedment is determined when designing shoring piers. I have tried reading through a few different resources, but I'm still pretty confused. Here are my parameters:
ka = coefficient of active earth pressure = 0.347
kp = coefficient of passive earth pressure = 2.045
H = height of excavation = 10 ft.
I'm assuming 12" deep piers spaced at 12" o.c., just to simplify things for this calcualtion.
Here is a list of the methods I've looked into:
1. I have RetainPro, and I used their Soldier Pile Retaining Wall module. The image below is the pressure distribution that they use.
2. I have been studying for the PE and the image below is the pressure distribution they show in the Civil Engineering Reference Manual.
3. I read through the California DOT trenching and shoring module and they show the following pressure distribution:
As far as I can tell, these are all saying something different for what embedment to use, but I could be wrong. Which of these are correct? I'll probably have some follow up questions once I know what a good starting point is for determining embedment on shoring piers.
ka = coefficient of active earth pressure = 0.347
kp = coefficient of passive earth pressure = 2.045
H = height of excavation = 10 ft.
I'm assuming 12" deep piers spaced at 12" o.c., just to simplify things for this calcualtion.
Here is a list of the methods I've looked into:
1. I have RetainPro, and I used their Soldier Pile Retaining Wall module. The image below is the pressure distribution that they use.
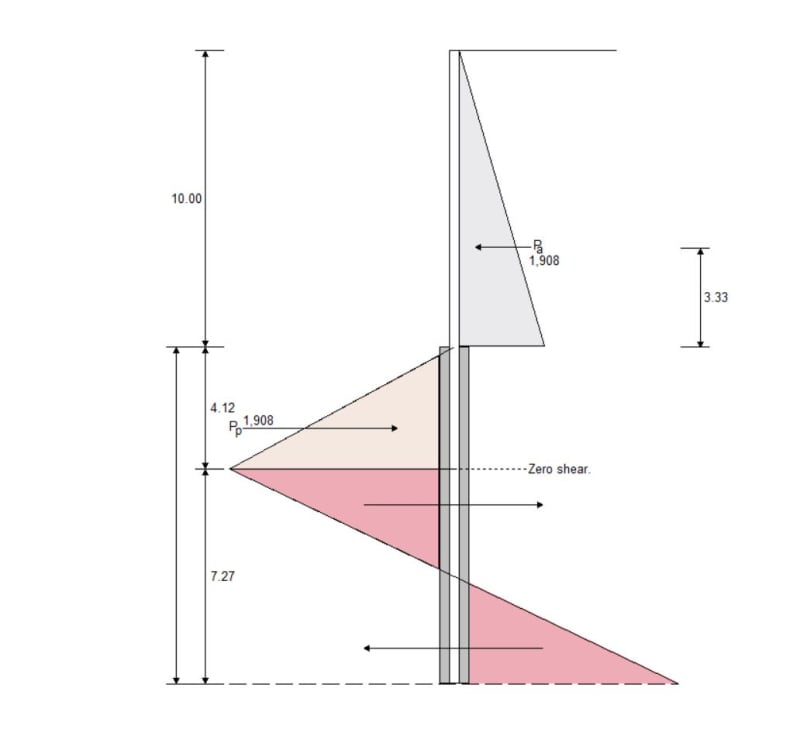
2. I have been studying for the PE and the image below is the pressure distribution they show in the Civil Engineering Reference Manual.
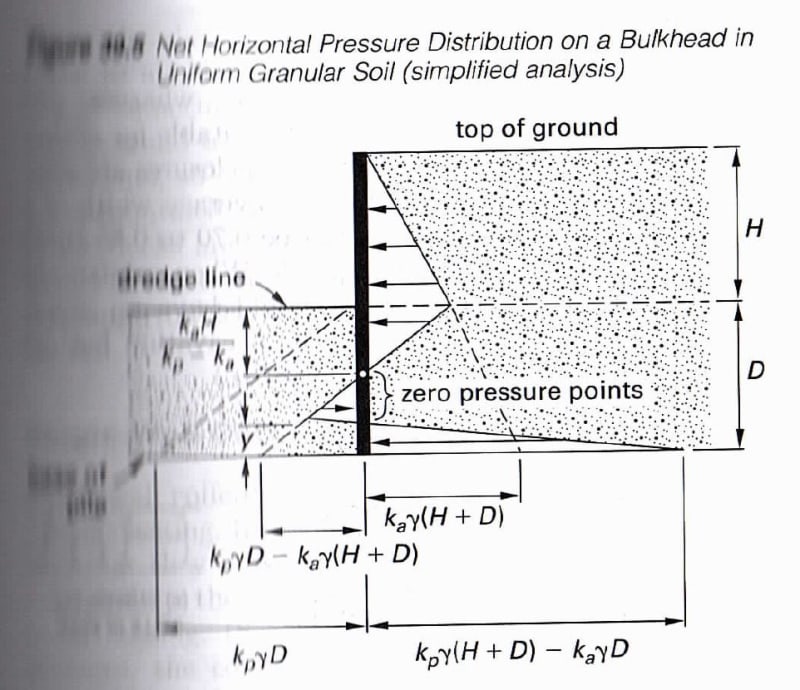
3. I read through the California DOT trenching and shoring module and they show the following pressure distribution:
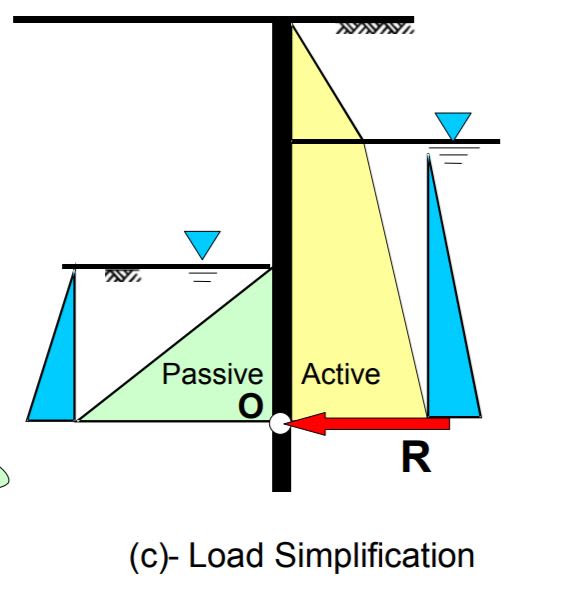
As far as I can tell, these are all saying something different for what embedment to use, but I could be wrong. Which of these are correct? I'll probably have some follow up questions once I know what a good starting point is for determining embedment on shoring piers.