Hi all,
I am trying to do a simulation where a hemispherical cup is placed into some sort of mold (see image). The cup is a little bit larger than the mold, and the idea is that the cup is forced in and deforms (in the plasticity range). Then, by friction the cup should stay in place. My goal is similair to this paper (but then in 3D) :Link
For this I use 4 repeating forces that 'hammer' the cup into the mold. However, my problem is that there is an initial distance (a gap) between the cup and the mold. Because of this, the cup only receives the hammering forces on one side and there is no equilibrium, and I get no covergence.
I was wondering what would be the best approach to solve this. If i model some elements that connect the parts it is not mimicing the reality anymore. As a boundary condition I use friction with a penaly formulation.
Any advice is much appreciated,
Kind regards
I am trying to do a simulation where a hemispherical cup is placed into some sort of mold (see image). The cup is a little bit larger than the mold, and the idea is that the cup is forced in and deforms (in the plasticity range). Then, by friction the cup should stay in place. My goal is similair to this paper (but then in 3D) :Link
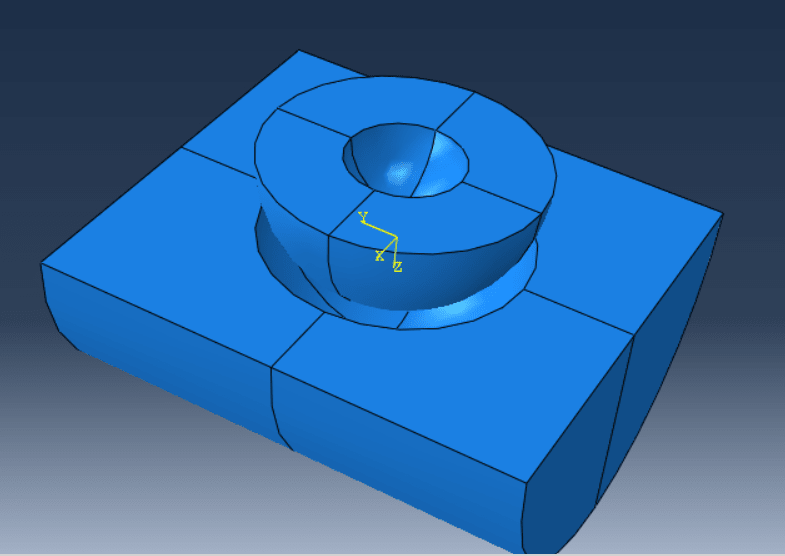
For this I use 4 repeating forces that 'hammer' the cup into the mold. However, my problem is that there is an initial distance (a gap) between the cup and the mold. Because of this, the cup only receives the hammering forces on one side and there is no equilibrium, and I get no covergence.
I was wondering what would be the best approach to solve this. If i model some elements that connect the parts it is not mimicing the reality anymore. As a boundary condition I use friction with a penaly formulation.
Any advice is much appreciated,
Kind regards