Hi,
Are there guidelines to implement single perturbation load vs scaled eigenmode perturbation from linear buckling for a nonlinear buckling analysis of pressure vessels (ASME Section VIII Div. 2, type 3 buckling)? PVT-17-1030 does a good job of summarizing different methods, but implementation of single perturbation methods appear to be suited for axial compression of composite cylinders. The software at work does not have the capability to input a scaled eigenmode shape to initiate buckling. Accordingly, is it appropriate to manually define a normal point load at the extremity of the buckled mode that would result in a perturbation that is equivalent to the manufacturing tolerance as shown? How can this manual approach be validated?
Additionally, are cut-outs, manway holes, service hatches, nozzle loads, eccentric loads, asymmetry, etc. sufficient features to initiate a non-linear buckling response without an initial perturbation?
Thank you.
Are there guidelines to implement single perturbation load vs scaled eigenmode perturbation from linear buckling for a nonlinear buckling analysis of pressure vessels (ASME Section VIII Div. 2, type 3 buckling)? PVT-17-1030 does a good job of summarizing different methods, but implementation of single perturbation methods appear to be suited for axial compression of composite cylinders. The software at work does not have the capability to input a scaled eigenmode shape to initiate buckling. Accordingly, is it appropriate to manually define a normal point load at the extremity of the buckled mode that would result in a perturbation that is equivalent to the manufacturing tolerance as shown? How can this manual approach be validated?
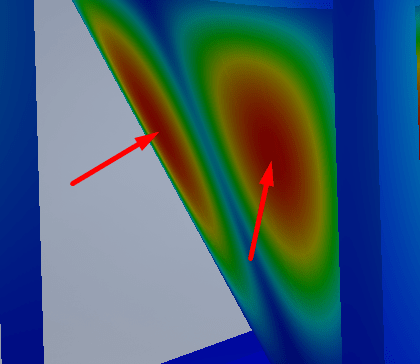
Additionally, are cut-outs, manway holes, service hatches, nozzle loads, eccentric loads, asymmetry, etc. sufficient features to initiate a non-linear buckling response without an initial perturbation?
Thank you.