Hello,
I decided to read about sheet metal design and manufacture principles for improving my design.
I have 2 questions I will be happy to be given answers to:
1. Bending orientation direction.
In which case I can afford a larger minimum radius?
2. Second question is regarding spring back and special tooling for coping with it.
I encountered this tooling, and I am not sure how it exactly works for coping with the spring back.
Thank you!
I decided to read about sheet metal design and manufacture principles for improving my design.
I have 2 questions I will be happy to be given answers to:
1. Bending orientation direction.
In which case I can afford a larger minimum radius?
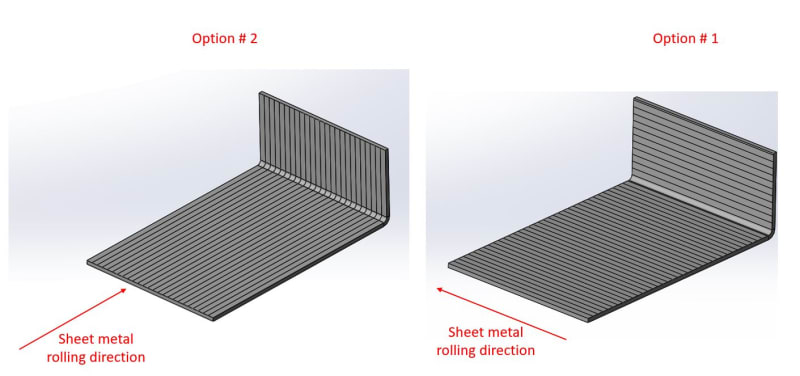
2. Second question is regarding spring back and special tooling for coping with it.
I encountered this tooling, and I am not sure how it exactly works for coping with the spring back.
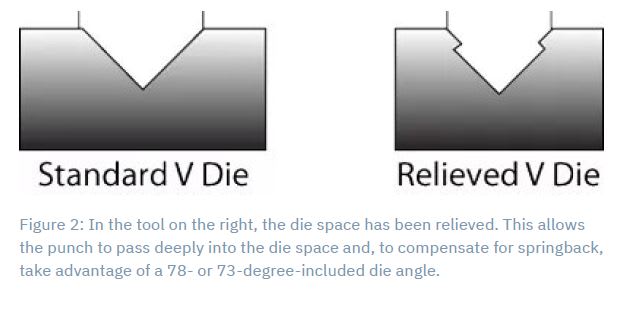
Thank you!