Hi
I have a machine in progress where i have a 200W 12vDC motor going thru a reduction box at 1:80 (final speed 27rmp) giving 40N.m ( 400kgf.CM )I am using an 11tooth 428 sprocket to drive a jackshaft off this reduction box.
I have a final lifting weight of 80kg which will be lifted by the final shaft. I would really like some help in sorting out what size sprockets i need to reduce the jackshaft speed and final drive to achieve this power. The final SPEED of the shaft is not that important its the lifting capacity i need.The final lifting shaft is attached to the drive chain from the jackshaft to the top sprocket. maybe this configuration is not the right one . do i need a further jackshaft somewhere ? i have a measurement problem where the outside dia of the very TOP sprocket cannot be more than 100mm (25T)
any and all comments and help massively appreciated
thankyou Richard
I have a machine in progress where i have a 200W 12vDC motor going thru a reduction box at 1:80 (final speed 27rmp) giving 40N.m ( 400kgf.CM )I am using an 11tooth 428 sprocket to drive a jackshaft off this reduction box.
I have a final lifting weight of 80kg which will be lifted by the final shaft. I would really like some help in sorting out what size sprockets i need to reduce the jackshaft speed and final drive to achieve this power. The final SPEED of the shaft is not that important its the lifting capacity i need.The final lifting shaft is attached to the drive chain from the jackshaft to the top sprocket. maybe this configuration is not the right one . do i need a further jackshaft somewhere ? i have a measurement problem where the outside dia of the very TOP sprocket cannot be more than 100mm (25T)
any and all comments and help massively appreciated
thankyou Richard
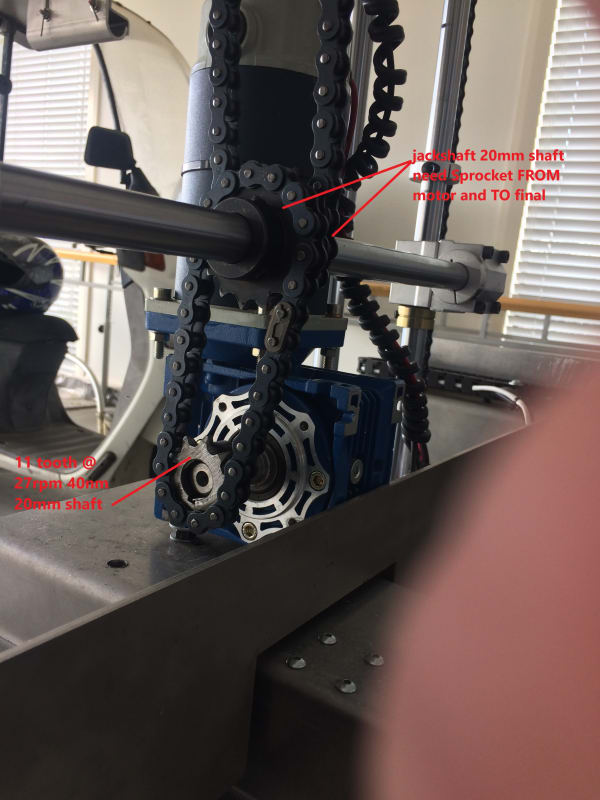
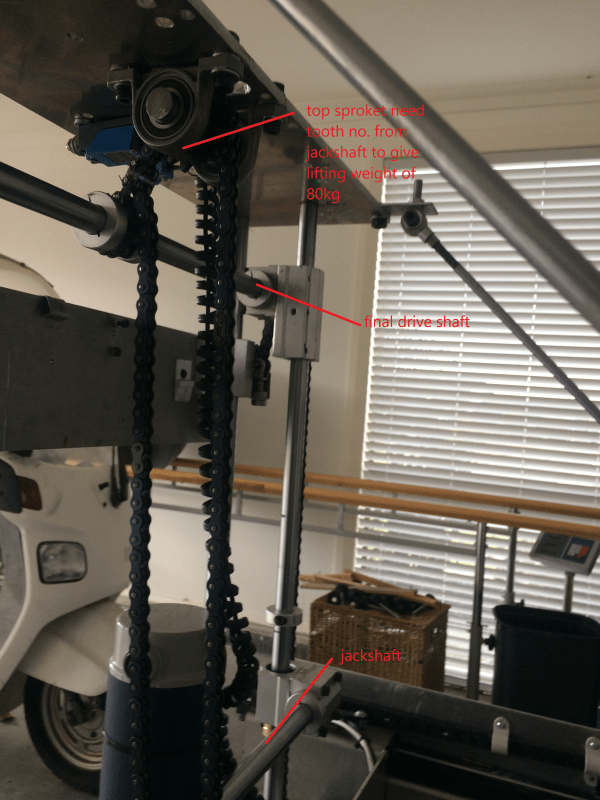
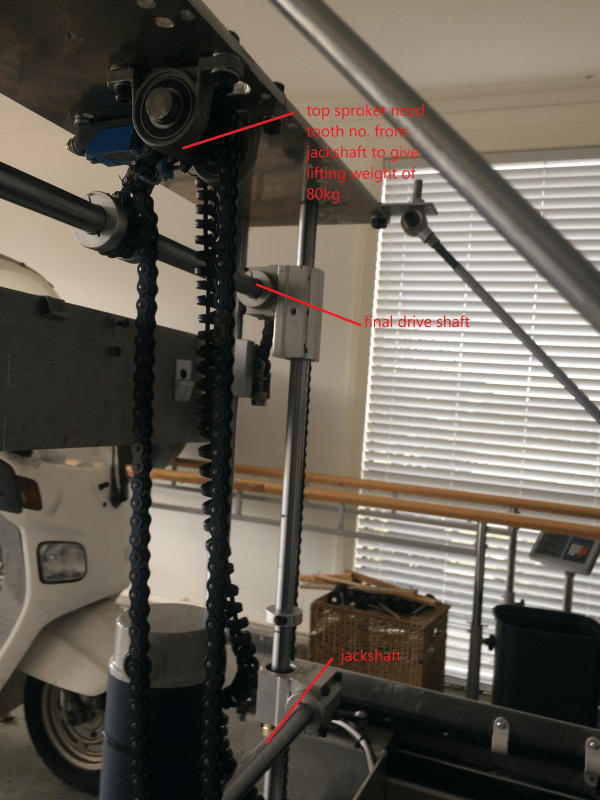
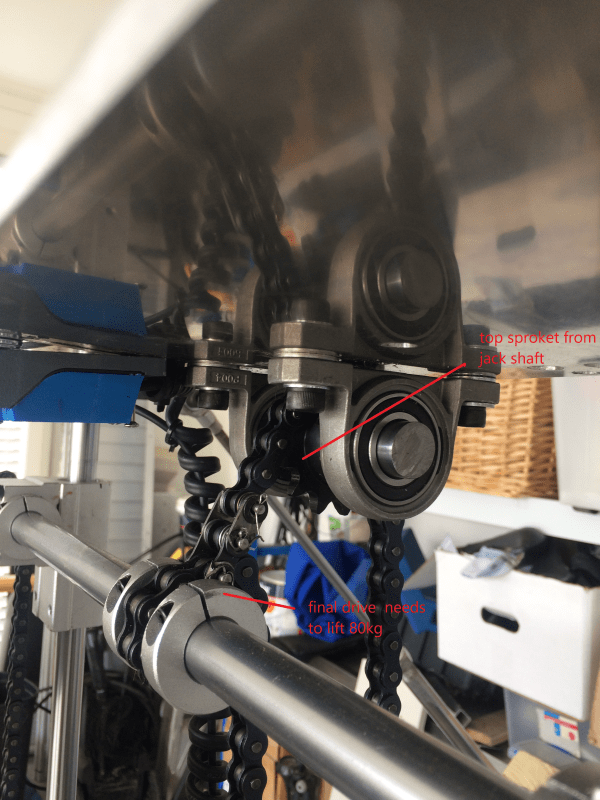