Hello everyone, I would like to make a square-to-round ducting and flat pattern it for laser cutting. The bend lines should originate from the square corners like the picture below done in Solidworks.
- I have used the through curves method, but that method does not show the bend lines in the flat pattern.
- Then I used the Lofted flange option in sheet metal, where you can set the total bend lines you want in the "bend segments" this method works great, as seen in photo 1 and 2 below.
Ths is exactly how I want the ducting to look like. When doing only half of the shape the lofted flange works great, but when doing it for the full shape and making a small cut-out before doing the lofted flange, the shape of the ducting is not what I want, as the bend lines are now everywhere instead of only from the square corners, can be seen below.
I have been struggling with this for a time now, it is such an irritation because SolidWorks can do this easily.
Any help will be much appreciated
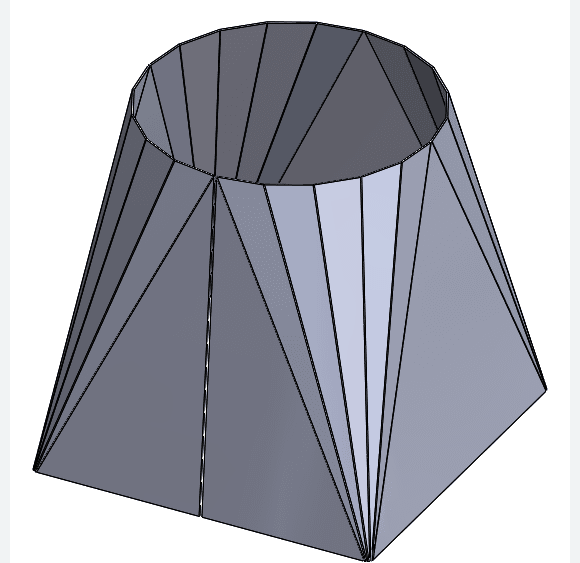
- I have used the through curves method, but that method does not show the bend lines in the flat pattern.
- Then I used the Lofted flange option in sheet metal, where you can set the total bend lines you want in the "bend segments" this method works great, as seen in photo 1 and 2 below.
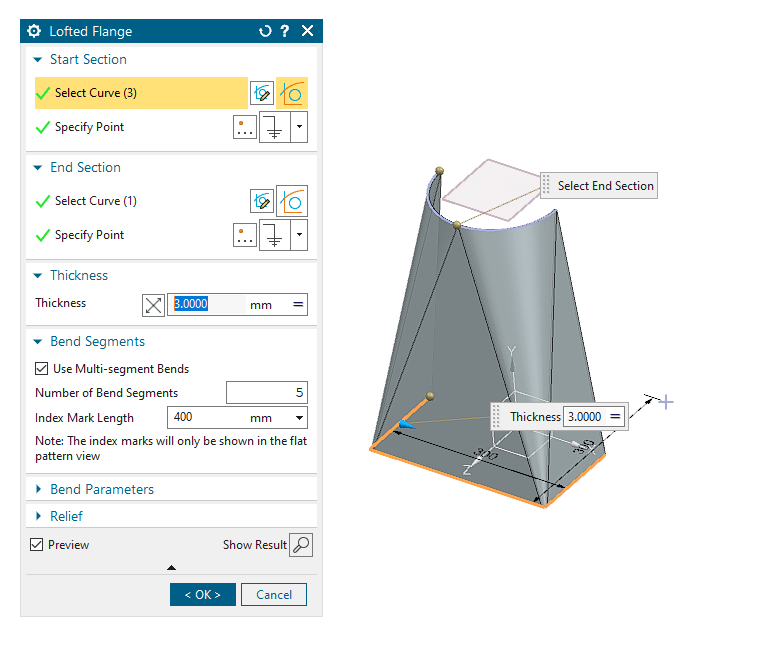
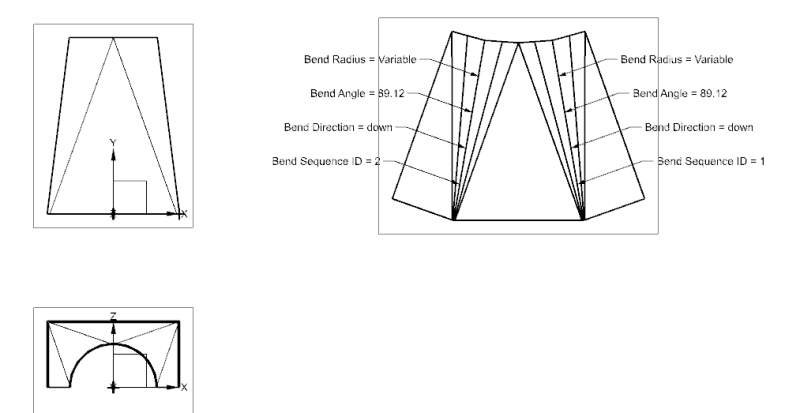
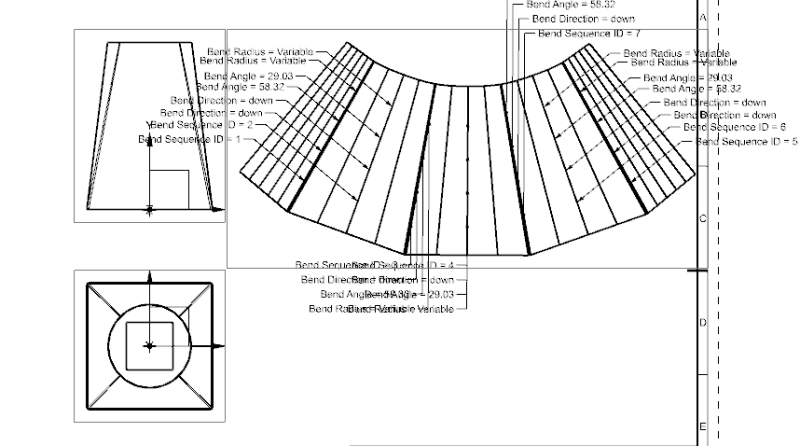
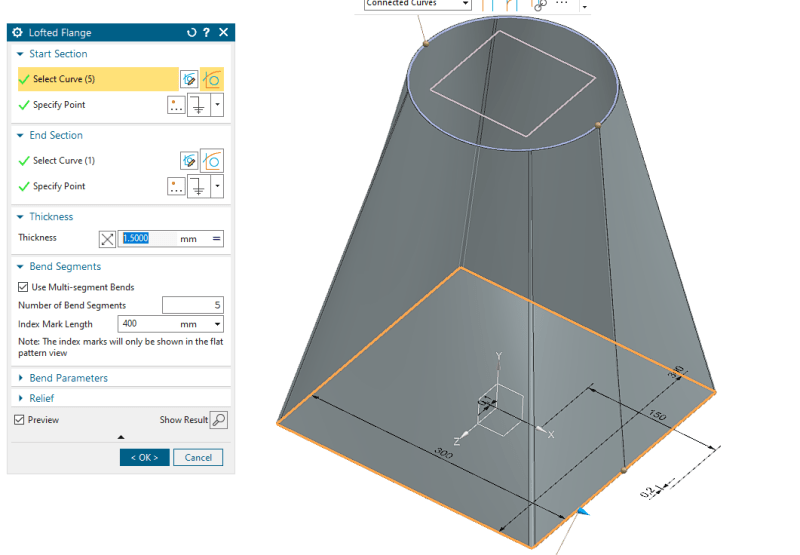
I have been struggling with this for a time now, it is such an irritation because SolidWorks can do this easily.
Any help will be much appreciated