We are exchanging a supply unit with several hydraulic pumps.
We have 3 pumps supplied through the same fuses 250A they each have their own motor breaker.
Previously it was a 11 kW, 5.5kW and a 0.75 kW.
The 0.75 kW only starts occasionally and very rarely.
The other 2 start almost simultaneously.
What I realized was that the 5.5 kW motor has been changed to a 11kw motor so all of a sudden we have startcurrent at 335A.
22,5x8=180 A, 19,6x7,9=155A, 180+155=335A
I have the possibility to delay the start of one of the 11 kW pumps so I thought I would figure out the starttime of the motor.
Unfortunately I don't have all the figures for the pump that starts first the one I can't delay. :-(
It's a screw flexcore pump and have a max pressure of 40 bar but my guess it will never be more the 5-6 bar
The data for the other pump that I can delay is this.
It is a gear pump max pressure 45 bar.
The Load torque came from this formula
The only thing I ain't sure off is the η : Hydraulic-mechanical efficiency could find any number for it so I put it to 0,75 not sure if that is correct?
I did find this calculator I used..
But it feels the time is so short?
So I found another formula but then I got super long start times, seemed even more unreasonable, turned out he had missed some parentheses.... but there were some reference to ABB...
And there I found this formula
Which gave me approximately the same result as the calculator (ca 0.06 s).
Tst = ((0.0583 + 0.00289)/177.5)*157 =0.054122986 s
But can this be correct
or am I missing something?
NAFO Sergeant Anna Gr 69th Sniffing Brigade
We have 3 pumps supplied through the same fuses 250A they each have their own motor breaker.
Previously it was a 11 kW, 5.5kW and a 0.75 kW.
The 0.75 kW only starts occasionally and very rarely.
The other 2 start almost simultaneously.
What I realized was that the 5.5 kW motor has been changed to a 11kw motor so all of a sudden we have startcurrent at 335A.
22,5x8=180 A, 19,6x7,9=155A, 180+155=335A
I have the possibility to delay the start of one of the 11 kW pumps so I thought I would figure out the starttime of the motor.
Unfortunately I don't have all the figures for the pump that starts first the one I can't delay. :-(
It's a screw flexcore pump and have a max pressure of 40 bar but my guess it will never be more the 5-6 bar
The data for the other pump that I can delay is this.
It is a gear pump max pressure 45 bar.
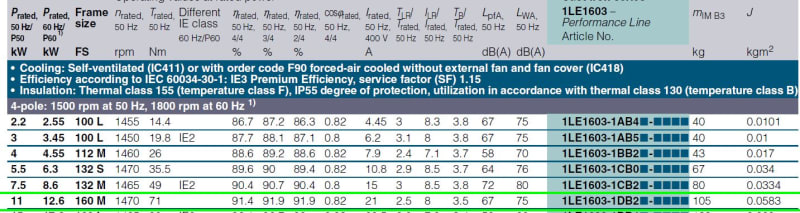
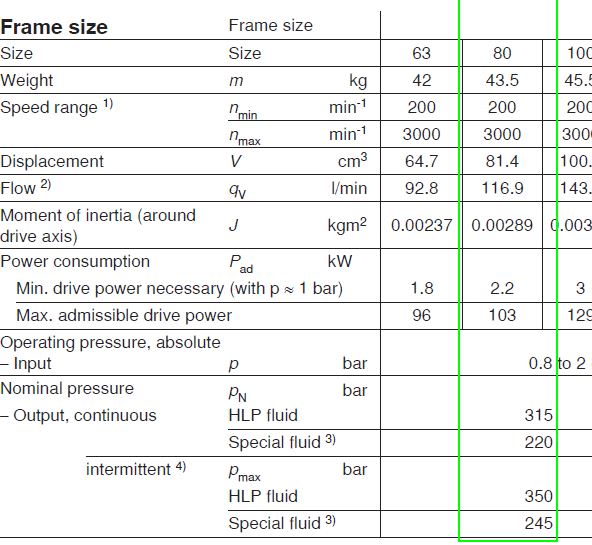
The Load torque came from this formula
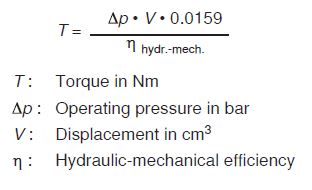
The only thing I ain't sure off is the η : Hydraulic-mechanical efficiency could find any number for it so I put it to 0,75 not sure if that is correct?
I did find this calculator I used..

But it feels the time is so short?
So I found another formula but then I got super long start times, seemed even more unreasonable, turned out he had missed some parentheses.... but there were some reference to ABB...
And there I found this formula
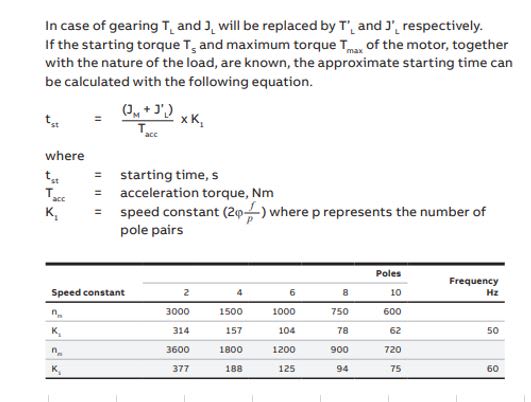
Which gave me approximately the same result as the calculator (ca 0.06 s).
Tst = ((0.0583 + 0.00289)/177.5)*157 =0.054122986 s
But can this be correct
![[ponder] [ponder] [ponder]](/data/assets/smilies/ponder.gif)
NAFO Sergeant Anna Gr 69th Sniffing Brigade