Ben29
Structural
- Aug 7, 2014
- 324
I have a job where we are designing a steel support structure to be installed inside an existing medical office to support a new medical equipment apparatus. The apparatus will put a moment of 4.8 ft-k on the steel support beam. and the plate that it is all attached to cannot rotate more than 0.16 degrees. Existing conditions prevent us from hanging the apparatus from the exiting structure.
On top of this, the new beams (which range from 12ft - 14ft long) will need to be spliced so we can get them into the building.
Would you suggest using slip critical bolts on the flange plates for the splice? Can anyone refer me to a design guide for beam splice designs?
Here is a screen-shot of the steel support we are designing. The medical boom apparatus will be hung from the center area.
On top of this, the new beams (which range from 12ft - 14ft long) will need to be spliced so we can get them into the building.
Would you suggest using slip critical bolts on the flange plates for the splice? Can anyone refer me to a design guide for beam splice designs?
Here is a screen-shot of the steel support we are designing. The medical boom apparatus will be hung from the center area.
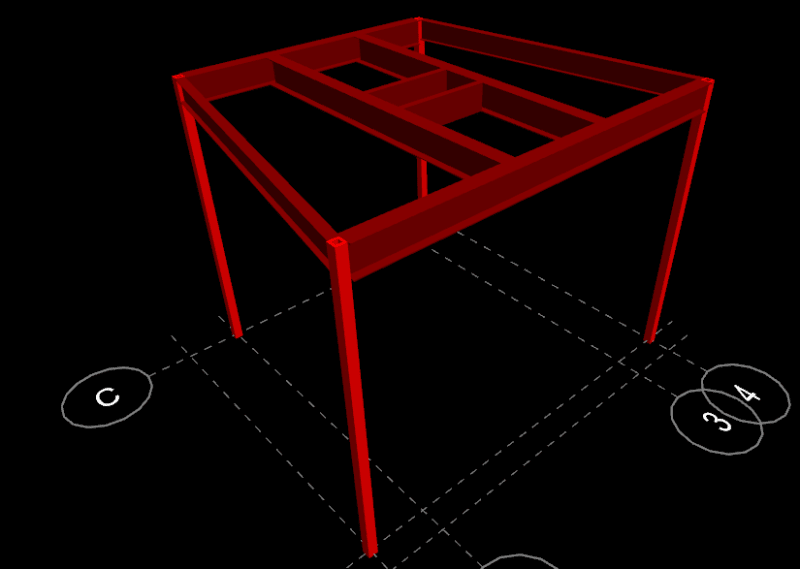