I live/work in the structural 'world' and need some assistance from EE's.
I work with unbonded post-tensioning strand tendons - basically high-tensile 7-wire carbon steel strands that are 'insulated' with HDPE sheath along there continuous length, and placed inside concrete slabs and beams and stressed to 80% of their tensile strength.
Sometimes (often?) these strands get severed (drill holes, core machine etc) and fracture. Often the party that did the drilling does not report the incident or was not aware (?) and then a few days later somebody notices the end of the strand has exited the slab edge.
We are often tasked with determining the location of the break and probable cause, and eventual repair. Probable cause requires us to know the location of the break, and on a construction project site this can be challenging with HVAC/mech/elec sub on a project to determine whos fasteners/hole is to blame.
We usually resort to extracting the failed strand segment, then simply measure the extracted length and determine the failure location. But often this is very inconvenient (like the exterior of the 40th floor of a building).
There exists electrical equipment to determine electrical cable length measurement and 'shorts' using TDR. Would such devices work with 7-wire solid carbon steel strands, where access to only one end of the cable is available?
I am looking for precision/accuracy of say +/-1 foot.
A typical 7-wire strand is the following:
Thank you.
I work with unbonded post-tensioning strand tendons - basically high-tensile 7-wire carbon steel strands that are 'insulated' with HDPE sheath along there continuous length, and placed inside concrete slabs and beams and stressed to 80% of their tensile strength.
Sometimes (often?) these strands get severed (drill holes, core machine etc) and fracture. Often the party that did the drilling does not report the incident or was not aware (?) and then a few days later somebody notices the end of the strand has exited the slab edge.
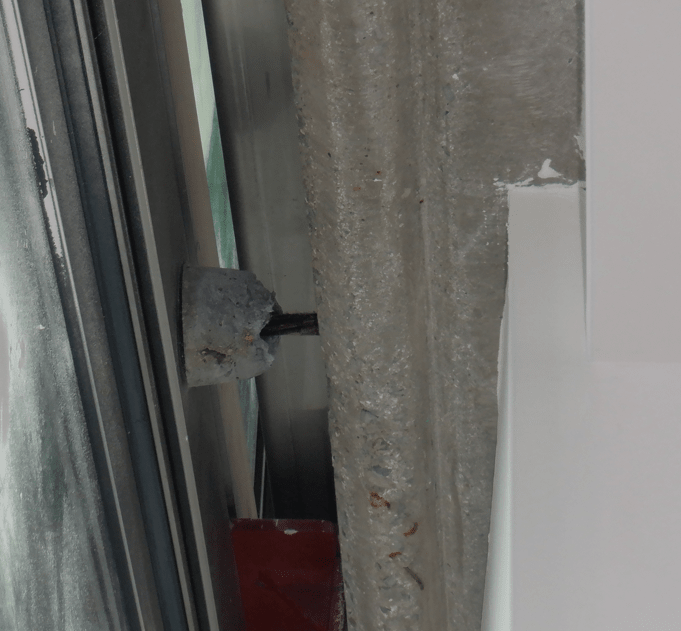
We are often tasked with determining the location of the break and probable cause, and eventual repair. Probable cause requires us to know the location of the break, and on a construction project site this can be challenging with HVAC/mech/elec sub on a project to determine whos fasteners/hole is to blame.
We usually resort to extracting the failed strand segment, then simply measure the extracted length and determine the failure location. But often this is very inconvenient (like the exterior of the 40th floor of a building).
There exists electrical equipment to determine electrical cable length measurement and 'shorts' using TDR. Would such devices work with 7-wire solid carbon steel strands, where access to only one end of the cable is available?
I am looking for precision/accuracy of say +/-1 foot.
A typical 7-wire strand is the following:
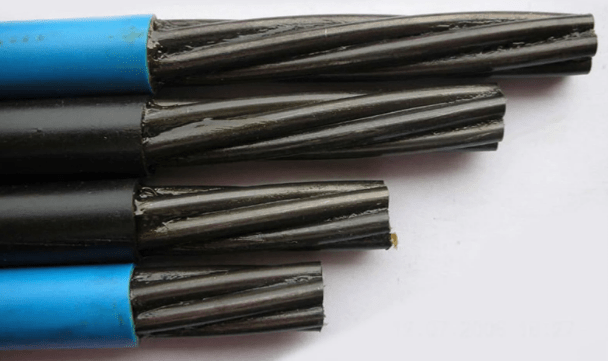
Thank you.