nivoo_boss
Structural
Hey everyone!
So I have to design a steel platform that's going to be used for supporting large log grapples for maintentance. The grapple weighs 150 kN or around 15 t. I'm thinking about applyling four point loads to the structure which arise from the grapple legs. But my main question is how to apply these loads to the beams supporting the grapple legs? Should they be angled relative to the cross-section or not? Pictures below with explanations.
1) Basically the situation looks like on this picture.
2) My current calculation model in SCIA Engineer.
3) Close-up of a beam cross-section with two vertical point loads. One point load is equal to 150/4=37,5 kN. The beams are currently SHS150x150x8, so the eccentricity of the load is 75 mm.
4) And a close-up with an angled load.
So yeah, my main question is how does this grapple affect the side truss/beam. Is it going to push it outwards or inwards or something else.
Any help would be appreciated.
So I have to design a steel platform that's going to be used for supporting large log grapples for maintentance. The grapple weighs 150 kN or around 15 t. I'm thinking about applyling four point loads to the structure which arise from the grapple legs. But my main question is how to apply these loads to the beams supporting the grapple legs? Should they be angled relative to the cross-section or not? Pictures below with explanations.
1) Basically the situation looks like on this picture.
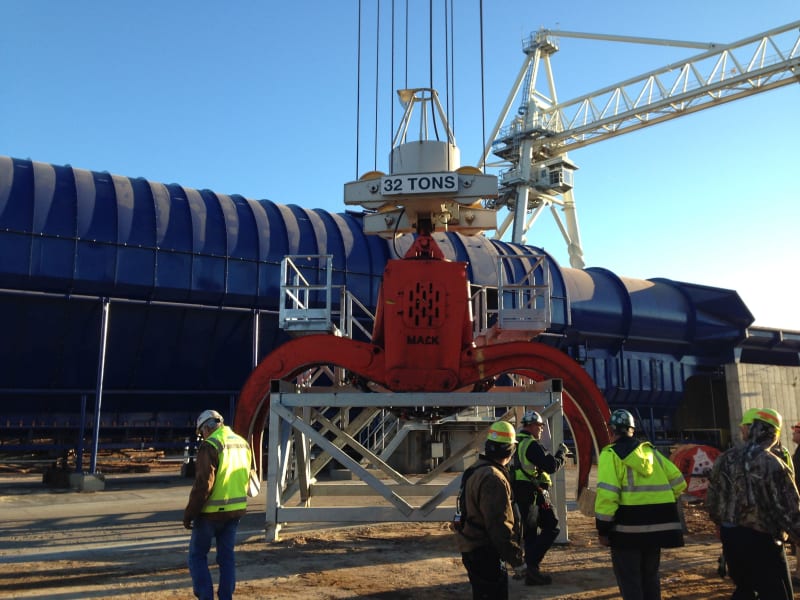
2) My current calculation model in SCIA Engineer.
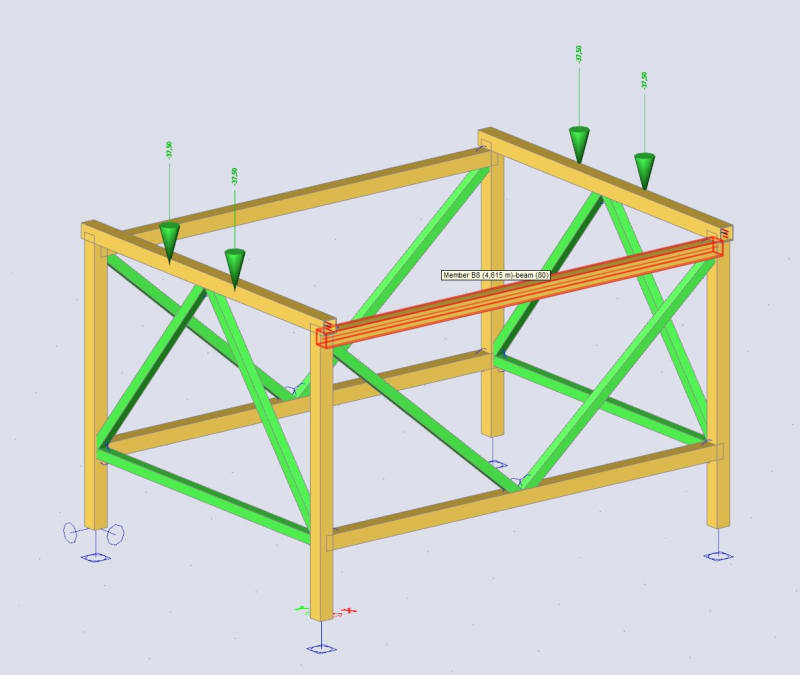
3) Close-up of a beam cross-section with two vertical point loads. One point load is equal to 150/4=37,5 kN. The beams are currently SHS150x150x8, so the eccentricity of the load is 75 mm.
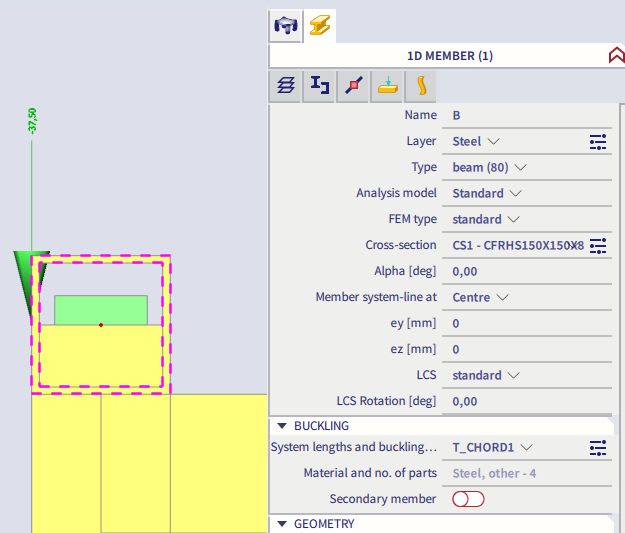
4) And a close-up with an angled load.
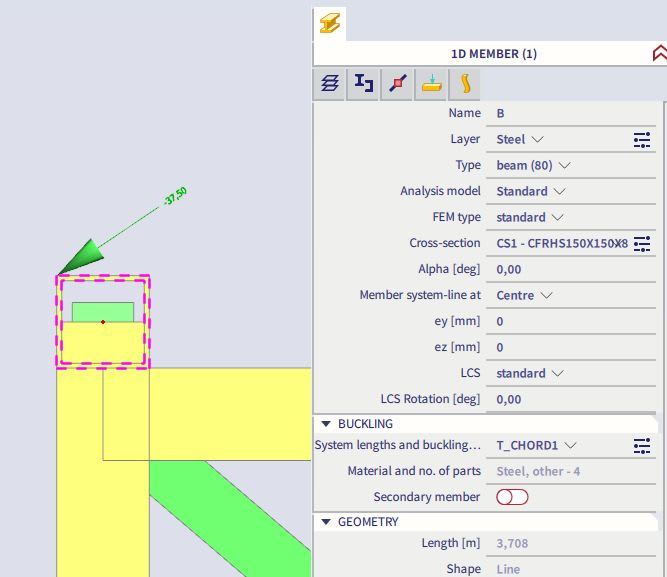
So yeah, my main question is how does this grapple affect the side truss/beam. Is it going to push it outwards or inwards or something else.
Any help would be appreciated.