I have an existing RC parapet that is 150 mm thick.
I would like to anchor a steel support to this parapet.
Steel support (beam) is a bearing seat for a timber beams along a parapet.
I have two options. Id like to hear from you what do you think/suggest.
OPTION 1
I have steel C section + stiffener (at a spot of concentrated load from timber beam). As far as I can see, there will be only shear forces in bolts. Correct?
What is bothering me is a fact, that a flanges are very short with this kind of steel profile. So a steel C section with height of 200 mm has only 75 mm long flanges. I dont need such big profile (height of section so its not really economical to choose big dimension just because of that). How much bearing seat is enough in your opinion?
OPTION 2
Bearing seat is not a problem, but what I dont like is the fact, I get tension forces in bolts. That is a problem since existing parapet is only 150 mm thick. Also reinforcement in parapet is at minimum.
What do you guys suggest? Have I overlooked something?
I would like to anchor a steel support to this parapet.
Steel support (beam) is a bearing seat for a timber beams along a parapet.
I have two options. Id like to hear from you what do you think/suggest.
OPTION 1
I have steel C section + stiffener (at a spot of concentrated load from timber beam). As far as I can see, there will be only shear forces in bolts. Correct?
What is bothering me is a fact, that a flanges are very short with this kind of steel profile. So a steel C section with height of 200 mm has only 75 mm long flanges. I dont need such big profile (height of section so its not really economical to choose big dimension just because of that). How much bearing seat is enough in your opinion?
OPTION 2
Bearing seat is not a problem, but what I dont like is the fact, I get tension forces in bolts. That is a problem since existing parapet is only 150 mm thick. Also reinforcement in parapet is at minimum.
What do you guys suggest? Have I overlooked something?
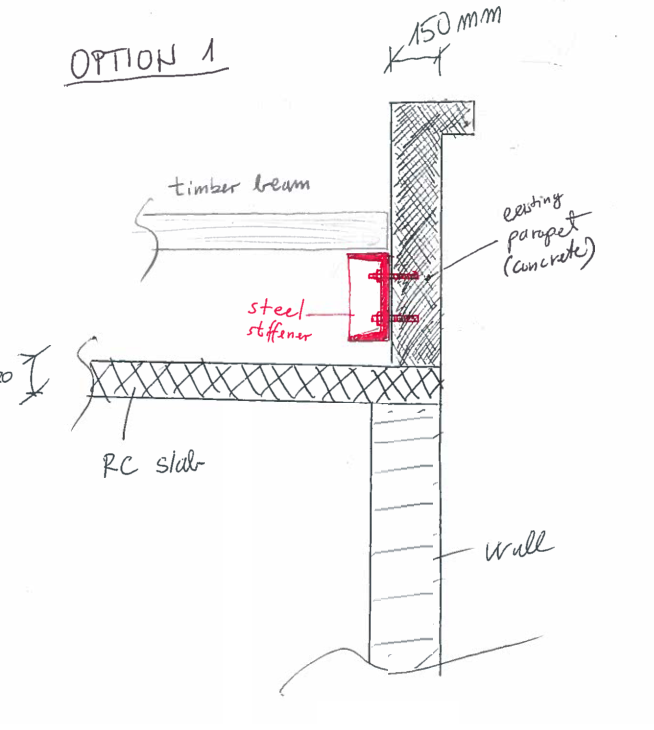
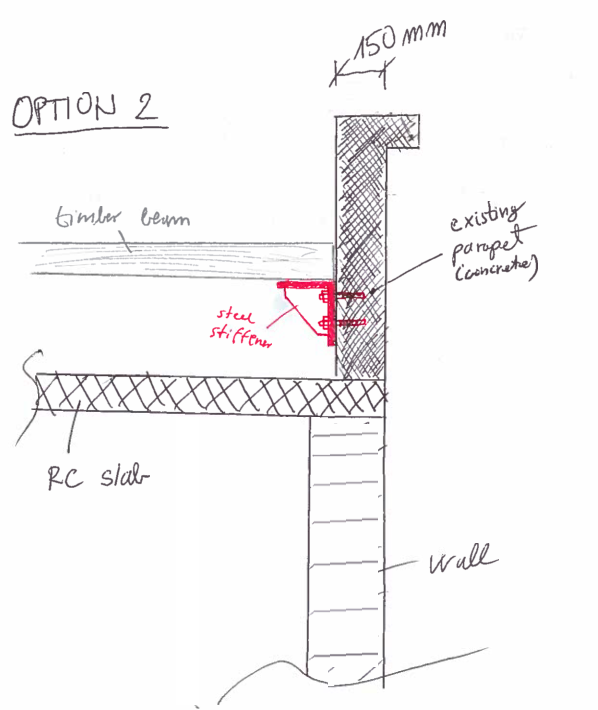
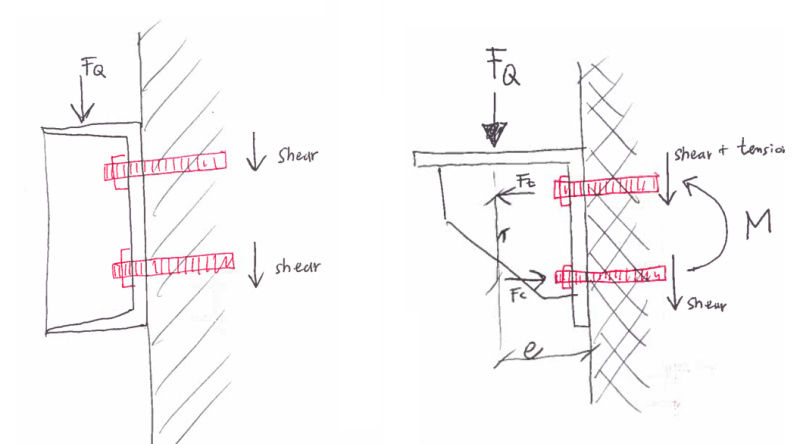