Hi all,
I want to discuss such type of connection where steel truss is welded to anchor plate installed on the top of concrete column. Steel truss is welded with fillet weld. It is considered that joint is rigid when truss post is welded around. My question is it possible to consider such joint as pinned or semi-rigid when welds are provided only on 2 sides?
I want to discuss such type of connection where steel truss is welded to anchor plate installed on the top of concrete column. Steel truss is welded with fillet weld. It is considered that joint is rigid when truss post is welded around. My question is it possible to consider such joint as pinned or semi-rigid when welds are provided only on 2 sides?
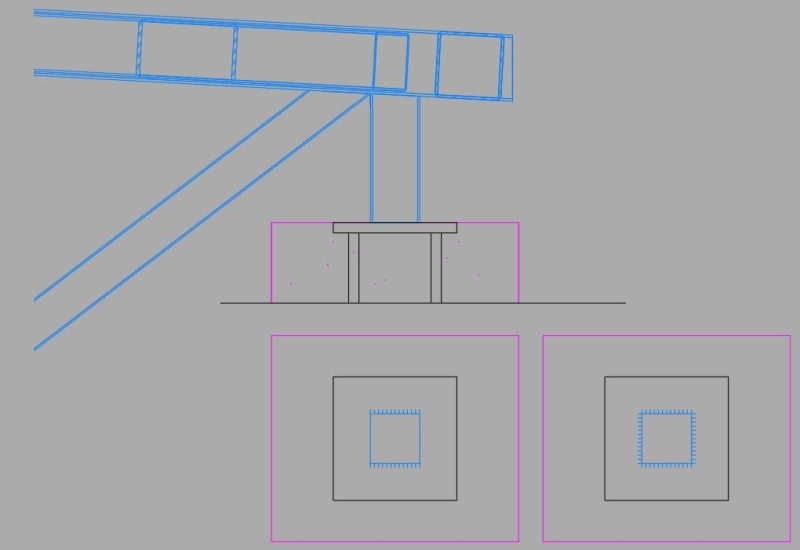