MOHAMMED89
Mechanical
I want to modify an existing vessel, Vessel Length 10m (T/T) And Dia 3.5m.
Saddle analysis is failing since the bending stress at the horn of saddle is failing for the operating case.
I have checked in in the Dennis-R-Moss, And is mentioned that stiffener can be provided to reduce the bending stress.
So i have run the PVElite calculation by proving the stiffener, Now the calculation is passing but i would like to know that the stiffener arrangement as per the attached sketch is acceptable or not.
Saddle analysis is failing since the bending stress at the horn of saddle is failing for the operating case.
I have checked in in the Dennis-R-Moss, And is mentioned that stiffener can be provided to reduce the bending stress.
So i have run the PVElite calculation by proving the stiffener, Now the calculation is passing but i would like to know that the stiffener arrangement as per the attached sketch is acceptable or not.
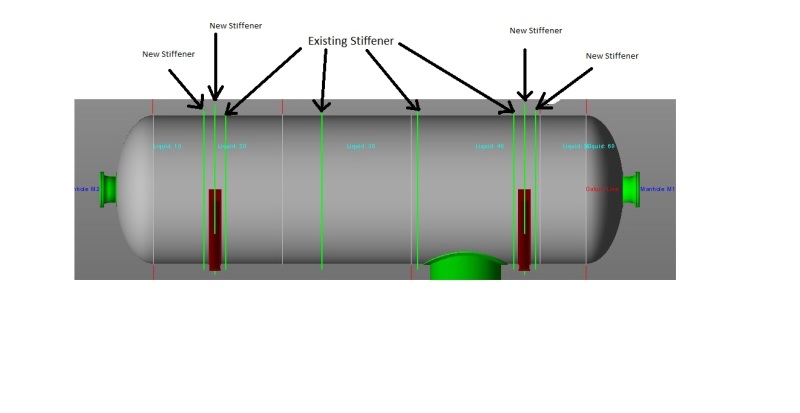