hello,
we have 2 plastic parts that should be bonded to each other with structural adhesive as described in the illustrative picture below:
I have to point out that all of the photos below aren't the exact design itself but an illustration I creadte very fast.
one of the concerns regarding this design was the adhesion interface that might be subjected to peeling due to bending as described in the illustrative picture below:
one of the solutions was adding another bonded part as described in the illustrative picture below:
The suggested manufacturing process is first bonding the added part while it has extra material outside and afterwards mutual machining.
The added part has to be with a small thickness, so the whole part might be able to be assembled in its destined place.
The mutual machining is for assuring the high precision that is critical.
Here is an illustrative description of the manufacturing process:
Now we are getting to the reason I am writing here - we had some argues about the end condition of the added bonded part.
1. one of the concepts is finishing with "zero" thickness that is optional due to the fact we have mutual machining.
The motivation was to get the best gradual stiffness transition, but some said the edge will be detached when finishing the machining process.
2. Another option was to have an end with a thickness of about 0.5 mm for not having a "zero" thickness end.
3. The last suggestion (that can't be accomplished since the added part isn't splitted but whole, but I still want to hear what you think) is having a kind of a face to face end with one of the parts:
I would like to hear what is your opinion.
As for now the leading option is he first one, and I am intrested to know if there is any risk in it.
if you have any guide book which deals in such issues - I will be happy to get a link.
Thanks!
we have 2 plastic parts that should be bonded to each other with structural adhesive as described in the illustrative picture below:
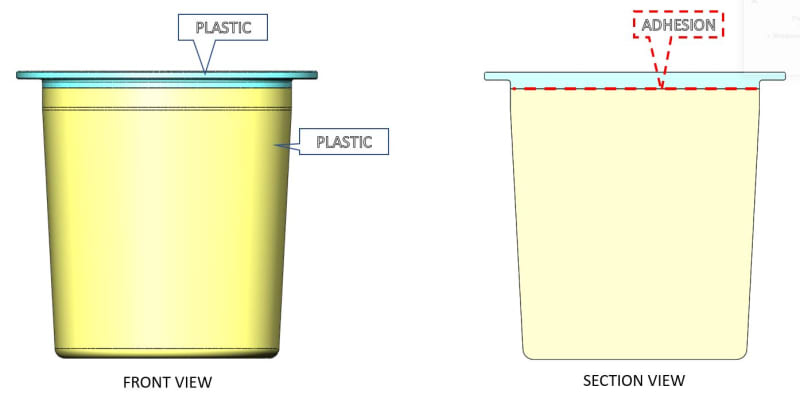
I have to point out that all of the photos below aren't the exact design itself but an illustration I creadte very fast.
one of the concerns regarding this design was the adhesion interface that might be subjected to peeling due to bending as described in the illustrative picture below:
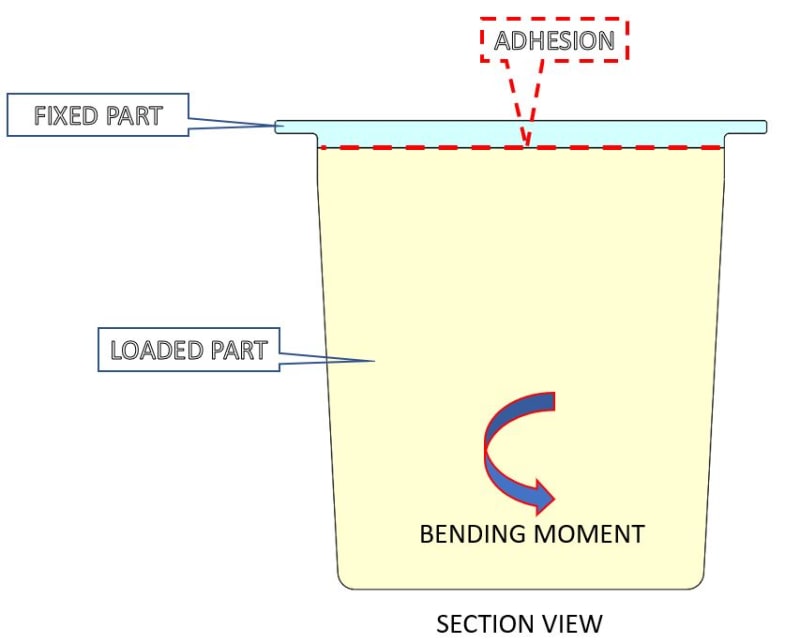
one of the solutions was adding another bonded part as described in the illustrative picture below:
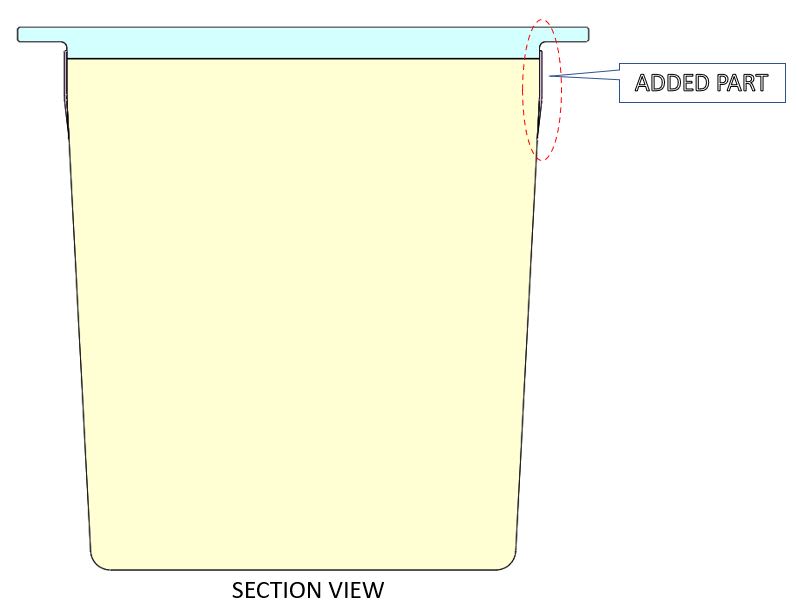
The suggested manufacturing process is first bonding the added part while it has extra material outside and afterwards mutual machining.
The added part has to be with a small thickness, so the whole part might be able to be assembled in its destined place.
The mutual machining is for assuring the high precision that is critical.
Here is an illustrative description of the manufacturing process:
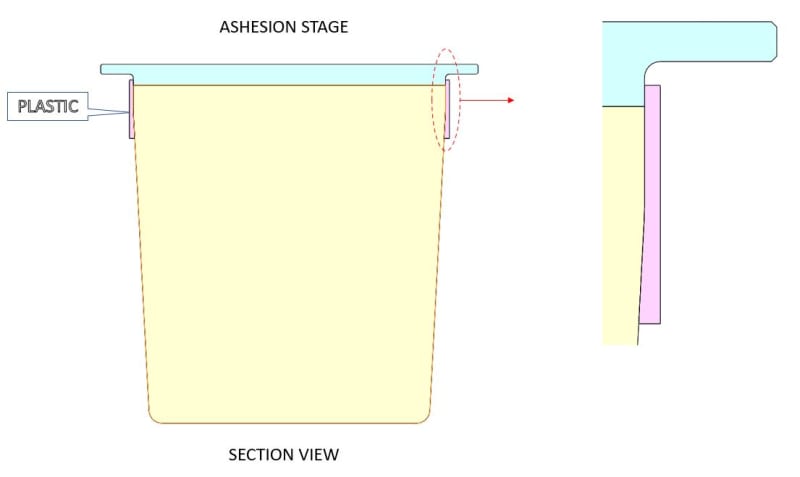
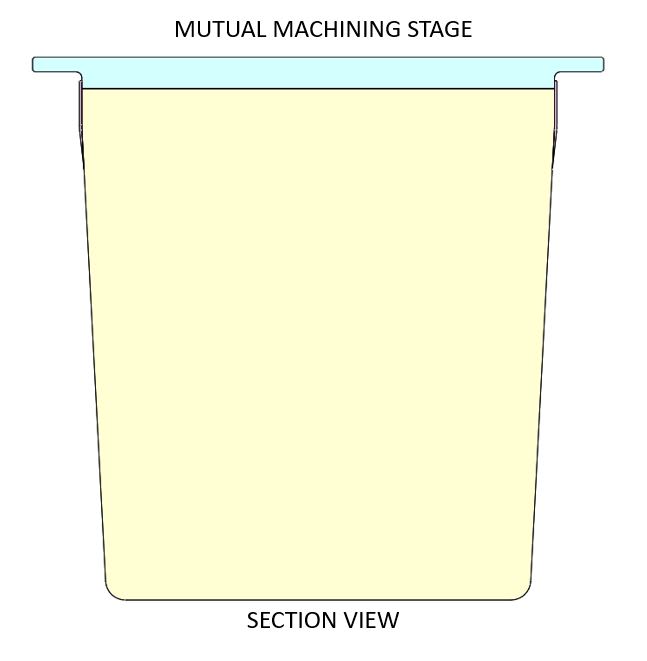
Now we are getting to the reason I am writing here - we had some argues about the end condition of the added bonded part.
1. one of the concepts is finishing with "zero" thickness that is optional due to the fact we have mutual machining.
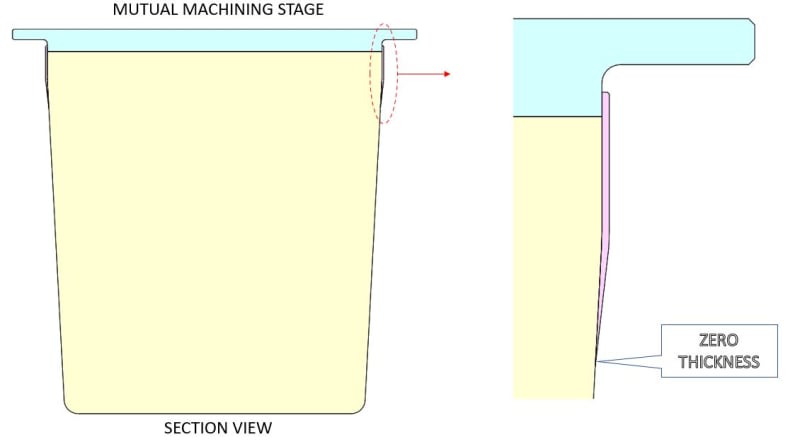
The motivation was to get the best gradual stiffness transition, but some said the edge will be detached when finishing the machining process.
2. Another option was to have an end with a thickness of about 0.5 mm for not having a "zero" thickness end.
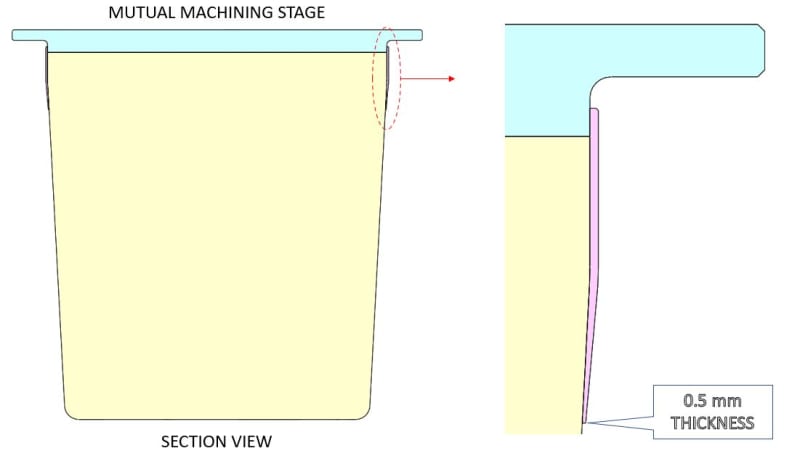
3. The last suggestion (that can't be accomplished since the added part isn't splitted but whole, but I still want to hear what you think) is having a kind of a face to face end with one of the parts:
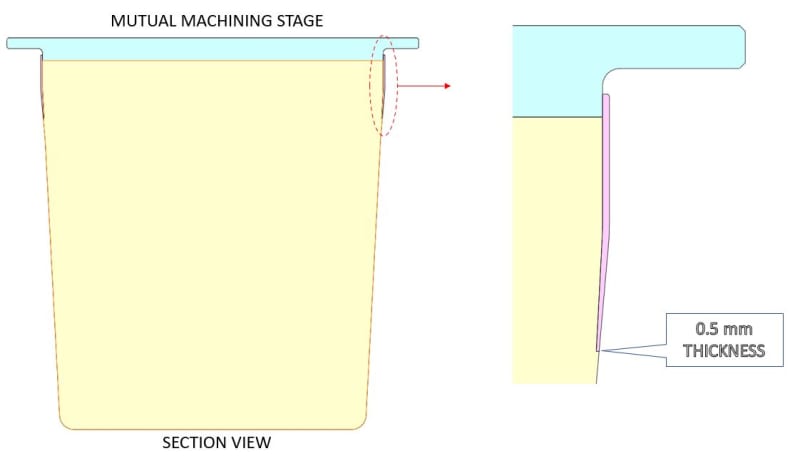
I would like to hear what is your opinion.
As for now the leading option is he first one, and I am intrested to know if there is any risk in it.
if you have any guide book which deals in such issues - I will be happy to get a link.
Thanks!