thatdanielxy
Mechanical
What's the correct understanding on below straightness definition?
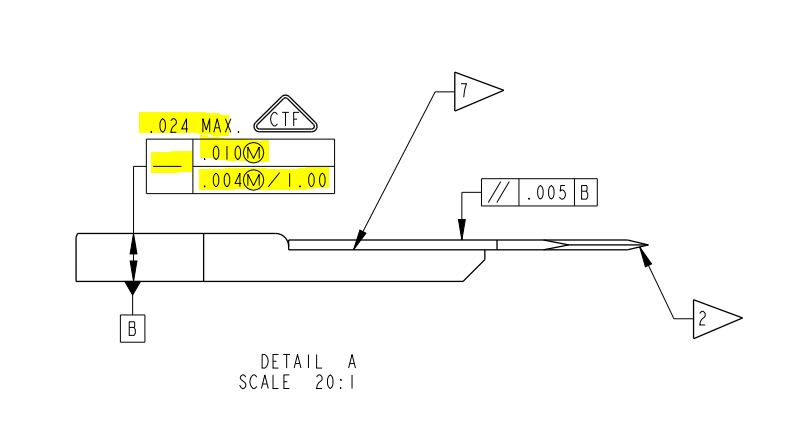
Follow along with the video below to see how to install our site as a web app on your home screen.
Note: This feature may not be available in some browsers.
CH said:Unfortunately the size is only given "open" one-way tolerance ("MAX") which makes it impossible to properly calculate virtual condition.
The size dimension needs both upper and lower tolerances for control to be fully legal.
I would say it is a maximum size dimension. That is my vote.CheckerHater said:what do you guys think .024 is - size, tolerance, or something else?
AndrewTT said:the leader goes directly to the FCF, which opens the door to interpreting the .024 MAX as some type of note
CheckerHater said:So, you believe the size specified is .000/.024? Does it have a meaning to you?
CH said:So, you believe the size specified is .000/.024? Does it have a meaning to you?