Hi,
I have a shaft (Ø10 mm, 210 mm long) I want to be straight. It passes through a 92 mm long bore. The worst case stack up shows the different in diameters to be 0.013 mm.
For simplicity I assumed constant curvature of any bending so I could apply this as a simple straightness (to axis) to the whole length. So 210 / 92 = 2.28, 2.28 x 0.013 = 0.03 mm.
The manufacturers are telling me this is tricky and if I can give them more. So I figured MMC (MMR actually because I'm an ISO guy) would help.
Problem is I've now scaled the straightness the MMC should also be scaled by the same amount, I assume there isn't a way to do this?
So I would have to use the strict definition of my straightness value, which is in the image below : [ - | Ø 0.013 / 92 (M) ]
I believe this is correct.
Technically the tolerance would only apply to the first 140mm section of the shaft.
How do I include a boundary condition of straightness (axis) over a length of a shaft?
This might all give them more in theory, but inspecting it is a completely different matter. MMC to straightness of an axis, hmmm maybe, now make that straightness over a sliding length, yikes. My CMM operator is not going to be happy.
Is it even worth the hassle...
I have a shaft (Ø10 mm, 210 mm long) I want to be straight. It passes through a 92 mm long bore. The worst case stack up shows the different in diameters to be 0.013 mm.
For simplicity I assumed constant curvature of any bending so I could apply this as a simple straightness (to axis) to the whole length. So 210 / 92 = 2.28, 2.28 x 0.013 = 0.03 mm.
The manufacturers are telling me this is tricky and if I can give them more. So I figured MMC (MMR actually because I'm an ISO guy) would help.
Problem is I've now scaled the straightness the MMC should also be scaled by the same amount, I assume there isn't a way to do this?
So I would have to use the strict definition of my straightness value, which is in the image below : [ - | Ø 0.013 / 92 (M) ]
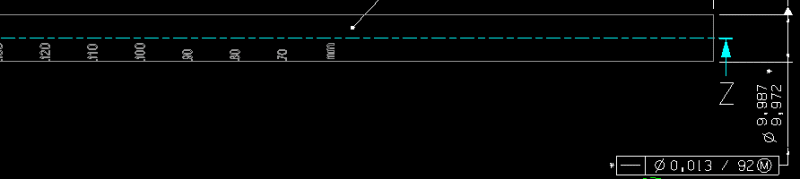
I believe this is correct.
Technically the tolerance would only apply to the first 140mm section of the shaft.
How do I include a boundary condition of straightness (axis) over a length of a shaft?
This might all give them more in theory, but inspecting it is a completely different matter. MMC to straightness of an axis, hmmm maybe, now make that straightness over a sliding length, yikes. My CMM operator is not going to be happy.
Is it even worth the hassle...