Hello,
I'm trying a model to simulate thermal stress distributions in each component in a 3-cell stack planar solid oxide fuel cell.
It consists of interconnect, sealing, porous nickel mesh, and PEN (positive electrode-electrolyte-negative electrode).
The analysis procedure is from 25°C to a high operating temperature (non-uniform temperature profile, between 650°C-800°C).
I can get the stress distributions at operating temperature, but I don't know how to use Abaqus to simulate the safety factor distribution if I have critical stresses of each component at 650, 700, 750, 800°C.
Sealing (25°C) and PEN are brittle materials, using maximum principal stress to assess failure criteria.
Sealing (650-800°C), interconnect, porous nickel mesh are ductile materials, using maximum Tresca equivalent stress to assess failure criteria.
Thanks.
I'm trying a model to simulate thermal stress distributions in each component in a 3-cell stack planar solid oxide fuel cell.
It consists of interconnect, sealing, porous nickel mesh, and PEN (positive electrode-electrolyte-negative electrode).
The analysis procedure is from 25°C to a high operating temperature (non-uniform temperature profile, between 650°C-800°C).
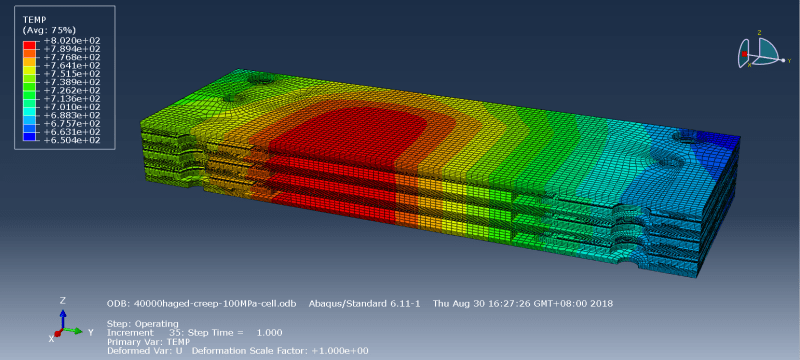
I can get the stress distributions at operating temperature, but I don't know how to use Abaqus to simulate the safety factor distribution if I have critical stresses of each component at 650, 700, 750, 800°C.
Sealing (25°C) and PEN are brittle materials, using maximum principal stress to assess failure criteria.
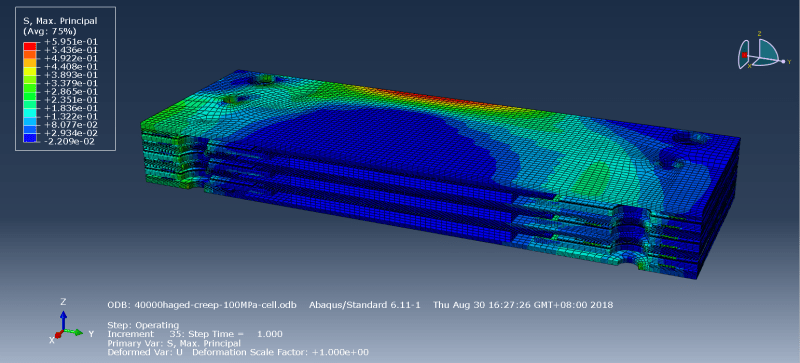
Sealing (650-800°C), interconnect, porous nickel mesh are ductile materials, using maximum Tresca equivalent stress to assess failure criteria.
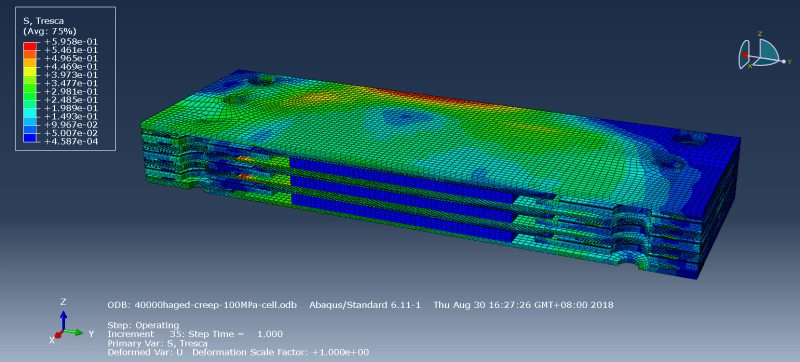
Thanks.